blakester
Silver Member
- Joined
- Jun 11, 2013
- Messages
- 114
hey everyone, thinking about building a forklift bin tipper for the harvest this year. I was basically going to copy the design of one for the most part. The big question for me is figuring out how to size the hydraulic rams. My thought was to pilfer the side shift hydraulic function on the forks to act as the tipper function. No idea what kind of psi the unit puts out, though i suppose i could find the specs online somewhere. What's the right way to calculate how much pushing power i need out of the system?
View attachment 518417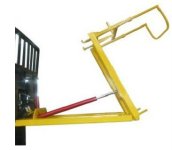
View attachment 518417
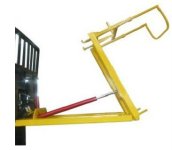