ovrszd
Epic Contributor
- Joined
- May 27, 2006
- Messages
- 33,499
- Location
- Missouri
- Tractor
- Kubota M9540, Ford 3910FWD, Ford 555A, JD2210
Finally got a table built. Well, until I start using it and discover it needs more things done to it.
Some materials I had onhand, some I bought. Tried to estimate the onhand costs. So end result price should be fairly close.
Top Plate 34"x60"x3/4" $230
40ft 2"x3"x1/8" tubing $75
5" casters 2 rigid/2swivel $75
Hitch Receiver $30
Misc Flat Iron $30
Misc Hardware $20
Total material cost $435
Estimate weight based on charts and guessing miscellaneous material 650lbs without the vice.
Blocked the plate level on the shop floor and basically built the table upside down until I had the legs finished and the casters added. Then flipped it over with the tractor and FEL to finish. Set the legs and frame in 3" from table top edge. Makes it less likely to stub one's toe on the legs and makes a great edge to clamp material and/or the welder ground.
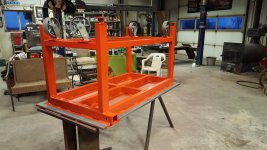
I used 1" bolts and nuts for the adjustable feet. Welded 4" diameter circle plates that I had laying around to the bolt heads. Hoping to absorb some of the shock on the concrete when beating the snot out of something on the table. Screw the feet down and lift the table off the casters and it's stationary. Want to move it, screw the feet up and it sits on the casters. I considered dreaming up some cool way to raise lower the casters but gave up and took the easy way out. Definitely wanted adjustable feet so I can level the table top for fabricating. Added a couple hangar rods for clamps, hammer, whatever else. Also added a sheet metal floor to the bottom shelf so I can pile a massive amount of scrap iron pieces on the table chassis.
The hitch receiver vice is so I can remove it if it's in the way during fabrication. Also so I can use the vice in other locations. Such as taking it with me when we go on offroad trips. We use the same receiver hitches on our buggies.
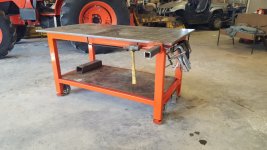
Then decided I wanted a cutting table addition. Or "burn table" as Shield Arc calls them. I had a piece of floor grate 24"x33" that would work great. Framed it with 2"x1/4" flatbar. Built a couple hinges to fasten it to the table end. Then went brain dead......
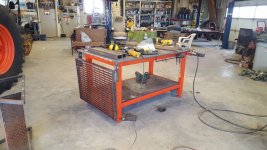
So I started a thread here about how to build the fasteners to hold the burn table in the upright position. I got a LOT of great help and ideas. Everyone's ideas were useable. After measuring my fabrication ability against the ideas I decided on folding braces. What a nightmare that turned out to be. Advanced mathematics was never my strong suit. By the way,,,,, did you know that the two arms of the folding brace MUST be the same length measuring from end bolt hole to the center hinge hole??? And,,,, did you know that the distance from the hinge bracket on the welding table to the bracket on the end of the burn table as well as the distance from the hinge bracket to the bracket on the leg MUST be the same???? I did not...... LD1 set me straight on that after the first hinged brace I built went into the scrap iron pile.
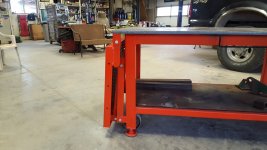
So, there she is guys. I expect this to work much better than the shop floor. I like the ability to easily move it so it's not killing floor space in the middle of the shop all the time. The casters work very, very well. Even after it's loaded with scrap steel I still expect it to easily be pushed around. I can move it with one hand now.
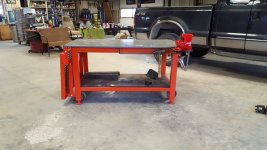
Some materials I had onhand, some I bought. Tried to estimate the onhand costs. So end result price should be fairly close.
Top Plate 34"x60"x3/4" $230
40ft 2"x3"x1/8" tubing $75
5" casters 2 rigid/2swivel $75
Hitch Receiver $30
Misc Flat Iron $30
Misc Hardware $20
Total material cost $435
Estimate weight based on charts and guessing miscellaneous material 650lbs without the vice.
Blocked the plate level on the shop floor and basically built the table upside down until I had the legs finished and the casters added. Then flipped it over with the tractor and FEL to finish. Set the legs and frame in 3" from table top edge. Makes it less likely to stub one's toe on the legs and makes a great edge to clamp material and/or the welder ground.
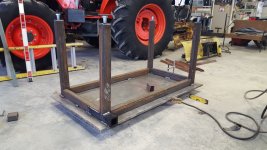
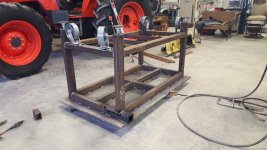
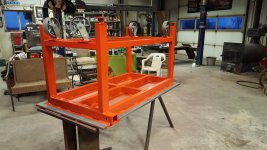
I used 1" bolts and nuts for the adjustable feet. Welded 4" diameter circle plates that I had laying around to the bolt heads. Hoping to absorb some of the shock on the concrete when beating the snot out of something on the table. Screw the feet down and lift the table off the casters and it's stationary. Want to move it, screw the feet up and it sits on the casters. I considered dreaming up some cool way to raise lower the casters but gave up and took the easy way out. Definitely wanted adjustable feet so I can level the table top for fabricating. Added a couple hangar rods for clamps, hammer, whatever else. Also added a sheet metal floor to the bottom shelf so I can pile a massive amount of scrap iron pieces on the table chassis.
The hitch receiver vice is so I can remove it if it's in the way during fabrication. Also so I can use the vice in other locations. Such as taking it with me when we go on offroad trips. We use the same receiver hitches on our buggies.

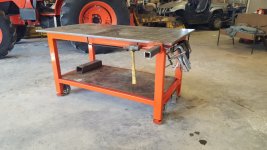
Then decided I wanted a cutting table addition. Or "burn table" as Shield Arc calls them. I had a piece of floor grate 24"x33" that would work great. Framed it with 2"x1/4" flatbar. Built a couple hinges to fasten it to the table end. Then went brain dead......
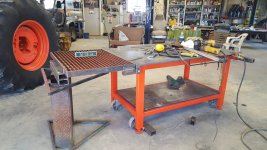
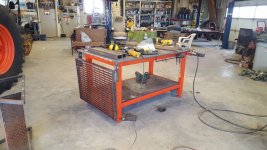
So I started a thread here about how to build the fasteners to hold the burn table in the upright position. I got a LOT of great help and ideas. Everyone's ideas were useable. After measuring my fabrication ability against the ideas I decided on folding braces. What a nightmare that turned out to be. Advanced mathematics was never my strong suit. By the way,,,,, did you know that the two arms of the folding brace MUST be the same length measuring from end bolt hole to the center hinge hole??? And,,,, did you know that the distance from the hinge bracket on the welding table to the bracket on the end of the burn table as well as the distance from the hinge bracket to the bracket on the leg MUST be the same???? I did not...... LD1 set me straight on that after the first hinged brace I built went into the scrap iron pile.
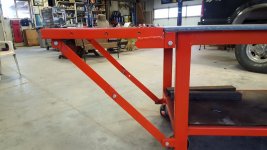
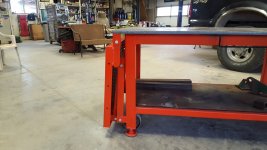
So, there she is guys. I expect this to work much better than the shop floor. I like the ability to easily move it so it's not killing floor space in the middle of the shop all the time. The casters work very, very well. Even after it's loaded with scrap steel I still expect it to easily be pushed around. I can move it with one hand now.
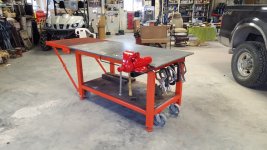
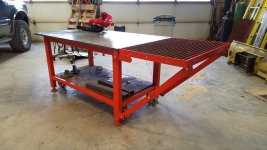
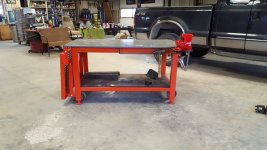