Sodo
Elite Member
- Joined
- Apr 21, 2012
- Messages
- 3,296
- Location
- Cascade Mtns of WA state
- Tractor
- Kubota B-series & Mini Excavator
I bought an old Massey Ferguson MF-31 Sickle mower for $150 (?). It was a challenge to get it going, the main wobble box shaft was broken and I welded it with my MIG. (Story Here)
I've been using it and decided that I like a sickle mower! Time to replace some wear parts though ("past" time!). I located the replacement guards and sickle knife sections at Webbs Sickle service and they were very helpful, but unable to provide the sickle-bar hold-down clips. So I bought the parts that they had, and resolved to keep looking for hold-down clips.
Well now the grass is growing, and I have not found any hold down clips, so decided to repair them. I know a bit more about welding cast iron now, but still wondered, if i'm just adding a wear-surface, why not see what happens just welding it with the MIG?
Welding cast steel with a MIG may be illegal in seventeen states but I did it anyway, and it's FINE !
Installed the new guards. Paint is worn off because this pic was after I used it.
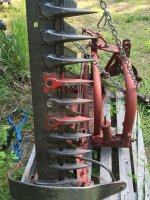
Heres a pic of the worn-out clips. You can see that the sickle bar is almost touching the bolts.
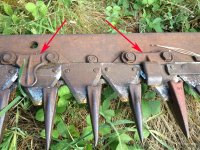
Ground off the rust and opened it up a little.
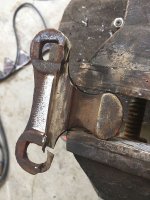
Welded a 1/4" rod into the worn out section of the clip. Also added some steel to the 'finger' on the hold-down clip.
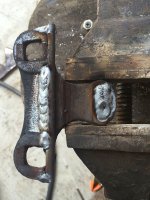
Ground it flat again.
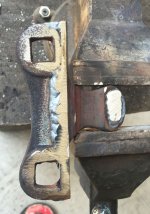
Here's what it looks like installed. I am on the lookout for replacement clips. But it's not all that urgent as the mower is working great.

I've been using it and decided that I like a sickle mower! Time to replace some wear parts though ("past" time!). I located the replacement guards and sickle knife sections at Webbs Sickle service and they were very helpful, but unable to provide the sickle-bar hold-down clips. So I bought the parts that they had, and resolved to keep looking for hold-down clips.
Well now the grass is growing, and I have not found any hold down clips, so decided to repair them. I know a bit more about welding cast iron now, but still wondered, if i'm just adding a wear-surface, why not see what happens just welding it with the MIG?
Welding cast steel with a MIG may be illegal in seventeen states but I did it anyway, and it's FINE !
Installed the new guards. Paint is worn off because this pic was after I used it.
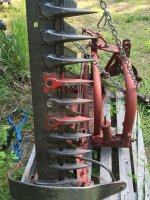
Heres a pic of the worn-out clips. You can see that the sickle bar is almost touching the bolts.
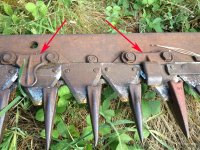
Ground off the rust and opened it up a little.
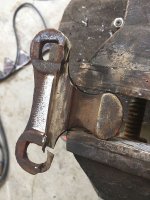
Welded a 1/4" rod into the worn out section of the clip. Also added some steel to the 'finger' on the hold-down clip.
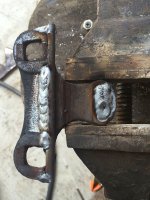
Ground it flat again.
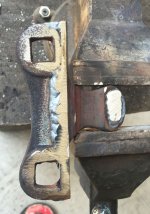
Here's what it looks like installed. I am on the lookout for replacement clips. But it's not all that urgent as the mower is working great.
