OP
boggen
Elite Member
- Joined
- Feb 22, 2011
- Messages
- 3,789
- Location
- Trivoli, IL
- Tractor
- SSTT (Sideways Snake Tain Tractor) and STB (sideways train box) tractor, dirt harvester
RECAP RECAP RECAP
see post 280 (post directly before this one) for a large listing of all diagrams / chicken scratches up to this point.
GOALS / PRO's / CON's....
==overall. grown tired, of extremely large size tractors going down the road, and then implements behind them. that more or less take up almost 2 lanes of road. or rather almost 16 foot width. (a single lane is approx 8 feet wide
==ya tractor power and implements can keep going up in power and size. but at what point before roads are no longer big enough, to allow for tractors to go down the roads without fully locking down the entire road for a few miles just to get tractor and implements from farm to field and from field to field.
==logistics. it takes a small organized crew to trailer and drive various tractors and implements here to there, and then hook everything up. before one can start operating in the field.
==all these wheels these implements tend to get, are just wheels on bearings. by the time ya add things up ya get up to 20 to 30 plus wheels. and maybe at most 12 of them are powered.
==on the rainy yuky muddy years, there is only a handful of days you can get out in the field, without tearing it up, this is part to just mud, but also weight of everything, and traction.
==reducing compaction, both simply rolling / driving over the field, but also how the plows, chisels, fertilizer, seeders, drills, discs, etc... physically work the soil.
==get a working tractor implement combo. that can fit within a 8 feet width (width of a road), 60 feet long (approx max length across the world), 14 feet tall (approx max height across the world) these road limit dimensions, are an attempt to be able to get the tractor / implement combo down the road, during all times of day, AND NIGHT!, vs being limited between 1 hour after sunrise, and 1 hour before sun set.
==road dimensions are more an attempt to make things more road safer.
==reduce logistics, of moving tractor/implements. reducing over all crew needed.
==go for multi use tractor implement unit, as in....tilling (working / preping soil for seeding/planting.), seeding / planting, and then harvesting the crop. as a complete single unit. that can do it all. and just change out implements.
==ability to handle multi different crops, from corn / beans row like crops, to potatoes, to celery, carrots that are more of a root based crop.
==ability to get through deep wet mud, regardless of tilling, seeding, harvesting.
==deal with fertilizers and chemicals while tilling / planting / harvesting. the on thing i am not looking at is once the crop begins to grow. and trying to go through fields, to spray a fertilizer or chemical. i am not completely knocking the idea out, but once the plant/crop size gets so large, you would be running over more plants and destroying them, vs a more dedicated spray/chemical unit most likely.
==adjust the fields, as in, move the soil around, like a motor grader, or box blade, or rear blade, or roll over scrapper, or dozer. both to fix fields up, but also maintain fields over the years. for good drainage, reduction of high and low spots.
==abilty for unit, to handle various degrees of slopes within the field. (unit needs flexible joints) so entire machine follows the ground contour.
==finite wheel control. as in down to .00001 or more .0000000001 in adjustments of RPM and torque. other words how many trucks/cars have some sort of traction control. this is more traction control for in the field. vs keeping car/truck on the road and not skidding out, or trying to stop as fast as possible. finite adjustments are for compaction, and easier ride, kinda of part of the suspension. with so many wheels / tracks on the ground. and most likely less weight. the need to adjust for wheel slippage, and tiny humps and dips. more finite control the more happier i will be. see attached images.
.......... 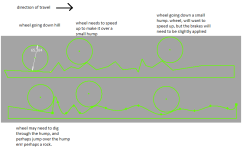
=======================
to meet above....
cab
==through out this entire thread, i have not really figured out a way to include a "cab" for a person to actual stand or seat to drive the unit. by the time you fold up all the implements, and placement for main engine, batteries, gas tanks, etc... you end up taking up a huge section. that would require extra linkages and things to move. in order to work around a cab.
==with above, i am more looking for a cab ((i am now calling it the ""command center"")), kinda like a tower command center at a big airport, or nasa space ship launch command center. but geared for 1 or 2 people. and have abilty to control multi tractor/implement combo units. other words a kids video game placed in a vehicle. and wireless internet connection to 1 to multi tractor/implement units.
==to add to above, it would be like playing with a RC (remote control) kids toy car. but being able to control multi RC cars from a single place.
==problem is internet more so wireless internet, make it satellite, to cell phone, to wisp, to other wireless internet, does not cover a good amount of areas, (dead zones) and the bandwidth, to handle multi video feeds/singles and sensor readings.
==with above, this is going to put the unit up into a upper tier, that will most likely require paying FCC a yearly fee, to use a certain frequency, that can handle say 5 miles radius from the "command center".
==i have not completely ruled out the idea, of tossing a "box" on end of a SSTT. to hold a person, for "safety". or having a chase or lead vehicle make it a truck, car, or 4 wheeler. that has either a pull cord safety rope when following, or some sort of rod that extends to 4 wheeler, for stopping unit completely.
==very old chicken scratch diagram...
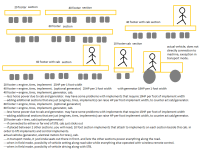
and now... more recent diagram...
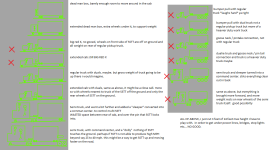
not covered in above, is low boy trailer. and not real keen on a low boy trailer. way to many hills and ditches, and simply not enough clearance.
other thing not covered, is treating SSTT as a wagon, much like a grain wagon. this still might be a good possibility.
================
wheel motors
==hydraulic motors for say in the rims of wheels (wheel hub motors), while yes they could work, i am having a hard time for the finite control. more so when needing to go between hydraulic control to electrical control, and then back to hydraulic control. and then dealing with hydraulic oil, that might have just the slightest amount of air entertained in the hyd oil. would cause reduction of finite control.
==electrical motors... on other hand there is no conversion between to power medium and feed back sensors. other words much faster response time. and more likely better finite control. but i am still not sold on current age typical regular electrical motors found out there in everyday life in factories, to vehicles, to other. while debate is still on, on type of electrical motor. to use in the rim of the wheels. i am more confident in saying electrical motors it will be.
==
==i would imagine sending power to both stator and rotor is going to require some extra electricity vs a regular motor that is just sending elec to just the rotor or just the stator. but i might be able to reduce amount of heat that is produced, by not having to ramp up the amps/volts in all the coils. well at least until full max torque is required, or full RPMs are required, and that is when other heat sources will more likely be more dominant in creation of heat.
==ya trade off is complexity for sending elec to both rotor and stator of motor. and in that more complex more prone to failures. but trade off of finite control for less wheel slippage in field, less compaction, less heat being created. it might work out for the better.
==if i read the rules/regs/laws correctly, electric motors will need to be made "explosion proof" other words in sure there is no chance for a spark to ignite a fume or dust. meaning electric motors can not have vents and air blown / pulled through them.
==since the electric motors will be submerged in mud / water. i can not rely on heat sink fins or external fan blowing air across the motor.
==i am left with coolant with a fluid. other words, just like your car / truck engine is cooled, the electrical wheel hub motors, will need some sort of water/antifreeze mix, flowing through it. to keep temperatures down.
==if i can keep a lower running temperature, of an electrical motor. that includes the full internals and externals. different magnets might be able to get used. to make stronger electric magnet. that spins the motor. stronger the magnetc, the more RPM's and torque, that might be possible from the motor. that is if i reading specs i have seen on the internet, for various types of permanent magnets, and there point of max heat before they start loosing there magnetic force.
================
brakes
with a switch from hydraulic motors to electric motors. electric magnetic clutch type of setup makes sense. and reducing need to run a higher PSI air hose down to the brakes.
=================
wheel types and how they are setup.
==this is now up in the air, more so looking at how the nasa spider looking rovor uses electric motors to move the linkages.
==at moment caster wheel design style has favor.
==old diagram
==the ability to sink the wheel past its center point / axle. and keep going. on a smaller diameter wheel. vs relying on 4 feet plus diameter wheels. is what has it.
==other wheel designs, seem to cause to much "junk" to stick out from the sides of a single wheel or 2 wheels mounted. and cause more stuff to drag and get hung up in the mud.
==i am leaning more towards "tracks" vs regular wheels. more so, if the nasa spider looking rover, electrical motors get used. the abilty to make a track to act like a "foot" and angle the track. so it does not run horizontal to the ground, but perhaps at a slight slope. so the track basically continually tries to climb up and out of the mud rut.
==track might be able to give a lower profile. instead of a 24" diameter wheel taking up 24 inches. a track i might be able to shave off a couple more inches to say 20 inches tall.
=======================
i am considering single direction of travel for the SSTT. (it has a rear and a front) for going through the field, vs UN-directional. if given implements connected allowed for it.
==i state above, due to wanting to move the center main frame of the SSTT to one side vs being straight down the middle.
==yet above is still not all there, i am tempted to almost completely remove a "main frame" that for most part stays in the same spot except for angling forward or backward for weight transferring. and in that, i am thinking of turning the so called main frame, more into multi linkages. were the implement and tires are linked directly together. and there would be multi tires and multi implements. and then just using main frame, more of as a bundle of wires, and hoses. and more act like a spinal cord going from ya brain, down to your butt.
==as much as i would like to place blamn on not wanting to deal with transport wheels, and removing them from the entire picture. and reduce things to less complexity of wheels and there linkages, and implements and there linkages. i am wanting something a tad more flexible.
======================
implements....
discs
==honestly considering putting a motor on them.
plows
==considering implementing something like no till drillers and air seeders, and other planters. and physically being able to control depth and cut angle.
chiseals and like
==considering full depth control like plows.
considering ughs" forget the name.. "plug aerators" like when aerating a lawn, and it takes small plugs up out of the ground.
==just wish there was a way, to make a small hole at the surface, and then go down a couple inches, and then "funnel" out to were roots for give crop would most likely go. suck that dirt up, and then put it back down into the upside down funnel hole. place seed and fertlizer in as the dirt all goes back in.
==================
actual engine, i am considering more of a stunt air plane type of engine. to better handle various angles the engine might be placed in.
running a hydrostatic transmission in a sense between engine and generator head. i am more thinking of "dynamic" output of the generator. if wheels are needing a specific frequency / pulse. instead of off setting all the changes at computer chip, help the computer chip out some. by turning generator a tad faster. or a tad slower.
though i am considering D/C for computer chips and sensors, but still producing A/C so i can send the A/C single directly to the motors. letting the computer chips change the A/C single as needed. the A/C sine wave, just seems to be more "good" i guess, in how an electric magnet would change from north pole to south pole. without sudden "stepping". a smoother directiontical change from north to south pole. vs trying to "smash" to steps together. i am not wanting surge of power struggle but a finite control of nice smooth changes in RPM's and torque for wheel motors.
though i am not completely sold, if i could produce a nice strong solid D/C single with little to no wave pattern from generator. i might be able to achieve higher finite micro stepping of volts/amps going into and out of the wheel hub motors. i am not sure if i want to place that much faith on banks of multi capacitors in a chip or on a PCB (programmable circuit board). to create a rapid frequency / pulse changes.
see post 280 (post directly before this one) for a large listing of all diagrams / chicken scratches up to this point.
GOALS / PRO's / CON's....
==overall. grown tired, of extremely large size tractors going down the road, and then implements behind them. that more or less take up almost 2 lanes of road. or rather almost 16 foot width. (a single lane is approx 8 feet wide
==ya tractor power and implements can keep going up in power and size. but at what point before roads are no longer big enough, to allow for tractors to go down the roads without fully locking down the entire road for a few miles just to get tractor and implements from farm to field and from field to field.
==logistics. it takes a small organized crew to trailer and drive various tractors and implements here to there, and then hook everything up. before one can start operating in the field.
==all these wheels these implements tend to get, are just wheels on bearings. by the time ya add things up ya get up to 20 to 30 plus wheels. and maybe at most 12 of them are powered.
==on the rainy yuky muddy years, there is only a handful of days you can get out in the field, without tearing it up, this is part to just mud, but also weight of everything, and traction.
==reducing compaction, both simply rolling / driving over the field, but also how the plows, chisels, fertilizer, seeders, drills, discs, etc... physically work the soil.
==get a working tractor implement combo. that can fit within a 8 feet width (width of a road), 60 feet long (approx max length across the world), 14 feet tall (approx max height across the world) these road limit dimensions, are an attempt to be able to get the tractor / implement combo down the road, during all times of day, AND NIGHT!, vs being limited between 1 hour after sunrise, and 1 hour before sun set.
==road dimensions are more an attempt to make things more road safer.
==reduce logistics, of moving tractor/implements. reducing over all crew needed.
==go for multi use tractor implement unit, as in....tilling (working / preping soil for seeding/planting.), seeding / planting, and then harvesting the crop. as a complete single unit. that can do it all. and just change out implements.
==ability to handle multi different crops, from corn / beans row like crops, to potatoes, to celery, carrots that are more of a root based crop.
==ability to get through deep wet mud, regardless of tilling, seeding, harvesting.
==deal with fertilizers and chemicals while tilling / planting / harvesting. the on thing i am not looking at is once the crop begins to grow. and trying to go through fields, to spray a fertilizer or chemical. i am not completely knocking the idea out, but once the plant/crop size gets so large, you would be running over more plants and destroying them, vs a more dedicated spray/chemical unit most likely.
==adjust the fields, as in, move the soil around, like a motor grader, or box blade, or rear blade, or roll over scrapper, or dozer. both to fix fields up, but also maintain fields over the years. for good drainage, reduction of high and low spots.
==abilty for unit, to handle various degrees of slopes within the field. (unit needs flexible joints) so entire machine follows the ground contour.
==finite wheel control. as in down to .00001 or more .0000000001 in adjustments of RPM and torque. other words how many trucks/cars have some sort of traction control. this is more traction control for in the field. vs keeping car/truck on the road and not skidding out, or trying to stop as fast as possible. finite adjustments are for compaction, and easier ride, kinda of part of the suspension. with so many wheels / tracks on the ground. and most likely less weight. the need to adjust for wheel slippage, and tiny humps and dips. more finite control the more happier i will be. see attached images.
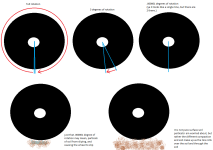
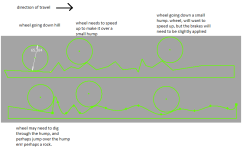
=======================
to meet above....
cab
==through out this entire thread, i have not really figured out a way to include a "cab" for a person to actual stand or seat to drive the unit. by the time you fold up all the implements, and placement for main engine, batteries, gas tanks, etc... you end up taking up a huge section. that would require extra linkages and things to move. in order to work around a cab.
==with above, i am more looking for a cab ((i am now calling it the ""command center"")), kinda like a tower command center at a big airport, or nasa space ship launch command center. but geared for 1 or 2 people. and have abilty to control multi tractor/implement combo units. other words a kids video game placed in a vehicle. and wireless internet connection to 1 to multi tractor/implement units.
==to add to above, it would be like playing with a RC (remote control) kids toy car. but being able to control multi RC cars from a single place.
==problem is internet more so wireless internet, make it satellite, to cell phone, to wisp, to other wireless internet, does not cover a good amount of areas, (dead zones) and the bandwidth, to handle multi video feeds/singles and sensor readings.
==with above, this is going to put the unit up into a upper tier, that will most likely require paying FCC a yearly fee, to use a certain frequency, that can handle say 5 miles radius from the "command center".
==i have not completely ruled out the idea, of tossing a "box" on end of a SSTT. to hold a person, for "safety". or having a chase or lead vehicle make it a truck, car, or 4 wheeler. that has either a pull cord safety rope when following, or some sort of rod that extends to 4 wheeler, for stopping unit completely.
==very old chicken scratch diagram...
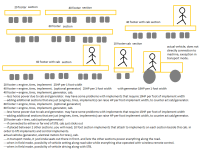
and now... more recent diagram...
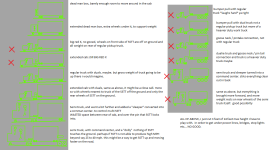
not covered in above, is low boy trailer. and not real keen on a low boy trailer. way to many hills and ditches, and simply not enough clearance.
other thing not covered, is treating SSTT as a wagon, much like a grain wagon. this still might be a good possibility.
see above diagram.Ryan I was thinking you were planning on equipment large enough to pay the not using a tractor. But hauling on pick up ?
================
wheel motors
==hydraulic motors for say in the rims of wheels (wheel hub motors), while yes they could work, i am having a hard time for the finite control. more so when needing to go between hydraulic control to electrical control, and then back to hydraulic control. and then dealing with hydraulic oil, that might have just the slightest amount of air entertained in the hyd oil. would cause reduction of finite control.
==electrical motors... on other hand there is no conversion between to power medium and feed back sensors. other words much faster response time. and more likely better finite control. but i am still not sold on current age typical regular electrical motors found out there in everyday life in factories, to vehicles, to other. while debate is still on, on type of electrical motor. to use in the rim of the wheels. i am more confident in saying electrical motors it will be.
==
i understand that, and would like to say i comprehend the statement as past that, and trying to apply fluid dynamics to the magnetic fields themselves being manipulated as the motor turns. i think there can be more finite control that can be had, beyond just sending electricity to just the stator or just to the rotor of an electrical motor. but by sending electricity to both rotor and stator at the same time and controlling frequency and pulse to both of them. in all sense i should be able to keep the frequency and pulse at a lower settings, vs cranking them up higher, if just sending elec to just stator or rotor, both for higher RPM's and torque.Elec. motors with dc voltage that is pulsed will rotate at full current and rpm is by frequency of pulse.
==i would imagine sending power to both stator and rotor is going to require some extra electricity vs a regular motor that is just sending elec to just the rotor or just the stator. but i might be able to reduce amount of heat that is produced, by not having to ramp up the amps/volts in all the coils. well at least until full max torque is required, or full RPMs are required, and that is when other heat sources will more likely be more dominant in creation of heat.
==ya trade off is complexity for sending elec to both rotor and stator of motor. and in that more complex more prone to failures. but trade off of finite control for less wheel slippage in field, less compaction, less heat being created. it might work out for the better.
==if i read the rules/regs/laws correctly, electric motors will need to be made "explosion proof" other words in sure there is no chance for a spark to ignite a fume or dust. meaning electric motors can not have vents and air blown / pulled through them.
==since the electric motors will be submerged in mud / water. i can not rely on heat sink fins or external fan blowing air across the motor.
==i am left with coolant with a fluid. other words, just like your car / truck engine is cooled, the electrical wheel hub motors, will need some sort of water/antifreeze mix, flowing through it. to keep temperatures down.
==if i can keep a lower running temperature, of an electrical motor. that includes the full internals and externals. different magnets might be able to get used. to make stronger electric magnet. that spins the motor. stronger the magnetc, the more RPM's and torque, that might be possible from the motor. that is if i reading specs i have seen on the internet, for various types of permanent magnets, and there point of max heat before they start loosing there magnetic force.
================
brakes
read this and like *duh* thanks ken!magnetic clutch no voltage full brakes.
with a switch from hydraulic motors to electric motors. electric magnetic clutch type of setup makes sense. and reducing need to run a higher PSI air hose down to the brakes.
=================
wheel types and how they are setup.
==this is now up in the air, more so looking at how the nasa spider looking rovor uses electric motors to move the linkages.
==at moment caster wheel design style has favor.
==old diagram

==the ability to sink the wheel past its center point / axle. and keep going. on a smaller diameter wheel. vs relying on 4 feet plus diameter wheels. is what has it.
==other wheel designs, seem to cause to much "junk" to stick out from the sides of a single wheel or 2 wheels mounted. and cause more stuff to drag and get hung up in the mud.
==i am leaning more towards "tracks" vs regular wheels. more so, if the nasa spider looking rover, electrical motors get used. the abilty to make a track to act like a "foot" and angle the track. so it does not run horizontal to the ground, but perhaps at a slight slope. so the track basically continually tries to climb up and out of the mud rut.
==track might be able to give a lower profile. instead of a 24" diameter wheel taking up 24 inches. a track i might be able to shave off a couple more inches to say 20 inches tall.
=======================
i am considering single direction of travel for the SSTT. (it has a rear and a front) for going through the field, vs UN-directional. if given implements connected allowed for it.
==i state above, due to wanting to move the center main frame of the SSTT to one side vs being straight down the middle.
==yet above is still not all there, i am tempted to almost completely remove a "main frame" that for most part stays in the same spot except for angling forward or backward for weight transferring. and in that, i am thinking of turning the so called main frame, more into multi linkages. were the implement and tires are linked directly together. and there would be multi tires and multi implements. and then just using main frame, more of as a bundle of wires, and hoses. and more act like a spinal cord going from ya brain, down to your butt.
==as much as i would like to place blamn on not wanting to deal with transport wheels, and removing them from the entire picture. and reduce things to less complexity of wheels and there linkages, and implements and there linkages. i am wanting something a tad more flexible.
======================
implements....
discs
==honestly considering putting a motor on them.
plows
==considering implementing something like no till drillers and air seeders, and other planters. and physically being able to control depth and cut angle.
chiseals and like
==considering full depth control like plows.
considering ughs" forget the name.. "plug aerators" like when aerating a lawn, and it takes small plugs up out of the ground.
==just wish there was a way, to make a small hole at the surface, and then go down a couple inches, and then "funnel" out to were roots for give crop would most likely go. suck that dirt up, and then put it back down into the upside down funnel hole. place seed and fertlizer in as the dirt all goes back in.
==================
actual engine, i am considering more of a stunt air plane type of engine. to better handle various angles the engine might be placed in.
running a hydrostatic transmission in a sense between engine and generator head. i am more thinking of "dynamic" output of the generator. if wheels are needing a specific frequency / pulse. instead of off setting all the changes at computer chip, help the computer chip out some. by turning generator a tad faster. or a tad slower.
though i am considering D/C for computer chips and sensors, but still producing A/C so i can send the A/C single directly to the motors. letting the computer chips change the A/C single as needed. the A/C sine wave, just seems to be more "good" i guess, in how an electric magnet would change from north pole to south pole. without sudden "stepping". a smoother directiontical change from north to south pole. vs trying to "smash" to steps together. i am not wanting surge of power struggle but a finite control of nice smooth changes in RPM's and torque for wheel motors.
though i am not completely sold, if i could produce a nice strong solid D/C single with little to no wave pattern from generator. i might be able to achieve higher finite micro stepping of volts/amps going into and out of the wheel hub motors. i am not sure if i want to place that much faith on banks of multi capacitors in a chip or on a PCB (programmable circuit board). to create a rapid frequency / pulse changes.
Last edited: