sd455dan
Elite Member
- Joined
- Oct 23, 2012
- Messages
- 4,737
- Location
- North Idaho
- Tractor
- Rhino 554, Ford 550 TLB (JD X500, MTD, Gilson riding mowers) Ford 3000-Sold
1st off this is not a well matched set of build parts for a press.
It is roughly copied from the HF 20 ton hydraulic press
I really wanted to use what I had laying around and most of this was pulled from the metal re-cycler pile.
So far -the only things purchased was a 4"x 4" x 72" square tube that will split to be used for the uprights and a 2 foot section of 7/8s round stock for the pins.
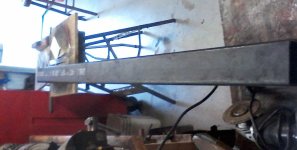
Thicker walled steel for the uprights would have been preferable, but the only square tubing that the local Pacific steel carries is only .188 walled and they didn't have C channel with the right dimensions either, so the 4x4 is what i ended up with to be split for the uprights.
It does (appear) to resemble what the HF 20 ton presses uprights are built from- but we don't have a store in town to measure them from and the info does not show up in their manuals either so it is what it is...
Here's a pic of some of what will be used to build it.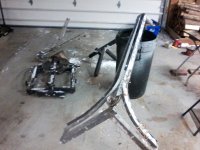
parts off junk garage door rails -plan on adding a hand winch to lift the aprons will salvage the cable pulleys, also need the springs to retract the hydraulic jack
old boat winch, will use to lift the aprons
part of a weight bench square tubing frame- think this will work for part of the base for the jack and guide between the uprights
Not shown,
several feet of 4"x 8" I beam for aprons and the top main frame support.
1 3/8" solid steel weight lifting bar and end pieces, thought this could be used for the main press shaft
1 1/2" bed frame C channel - a bit light but planning on using it for the uprights feet
1 BIG hydraulic jack- the others i have are nowhere near 20 ton , but this 1 is at least that, - plan is to plumb it at some point for a gauge and then work out the pressure.?. Right now don't have any big jobs planned for this press but don't want to break the uprights due to over stressing them.
It was Cold when starting on this,
12* in the shop when I laid out the 7/8" holes for the pins and scribed the lines to split the 4x4 in two.
Had warmed up to 26 when the hole drilling was done- Man drilling 32 holes in a row by hand is a work out
also began plasma cutting by splitting one side off of some of the 4 x 8 C channel and also splitting a 44 inch one in half to be used for front and back top plate pieces.
another little project in that picture- plasma cutting and shaping a piece of railroad rail into a small anvil, it should be handy
I was a bit concerned about firing up the plasma on my 3 in 1 machine in temps this low, but wanted to get going and thought that it might help to turn it on and let it idle for a couple minutes and then set the amps to just above minimum and lightly gouge a couple inches on the scribe line and warm the mosfets up a little bit before cranking it up to cut so that is what i did
It did a decent job of cutting the 4x4 piece into two but i left the very ends attached hoping to minimize warping, but even after letting it cool down there was some.
Next cut the bed frame rails and drilled holes in the uprights.
Welded the 2 trimmed 4 x 8 C channel together to form the top press piece with a void in the middle for the jack retract springs. Used 1/8 6011 and did my best to get full penetration in the gap between the 2 top plates added a piece of trimmed channel for where the jack seats on the top frame used 1/8 7018 for those welds.
Squared it up as much as I could ( sure would be nice to have a steel build table)
-Someday
and welded the uprights to the center piece with more 1/8 7018- also added the (feet) thought i took some pictures but can't find them.
Here's the basic frame standing
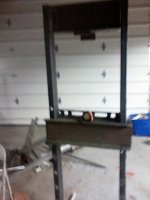
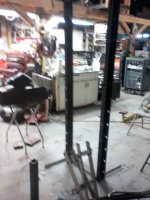
more to follow
It is roughly copied from the HF 20 ton hydraulic press
I really wanted to use what I had laying around and most of this was pulled from the metal re-cycler pile.
So far -the only things purchased was a 4"x 4" x 72" square tube that will split to be used for the uprights and a 2 foot section of 7/8s round stock for the pins.
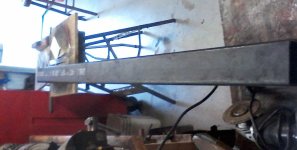
Thicker walled steel for the uprights would have been preferable, but the only square tubing that the local Pacific steel carries is only .188 walled and they didn't have C channel with the right dimensions either, so the 4x4 is what i ended up with to be split for the uprights.
It does (appear) to resemble what the HF 20 ton presses uprights are built from- but we don't have a store in town to measure them from and the info does not show up in their manuals either so it is what it is...
Here's a pic of some of what will be used to build it.
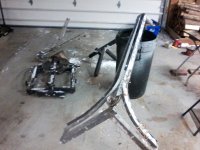
parts off junk garage door rails -plan on adding a hand winch to lift the aprons will salvage the cable pulleys, also need the springs to retract the hydraulic jack
old boat winch, will use to lift the aprons
part of a weight bench square tubing frame- think this will work for part of the base for the jack and guide between the uprights
Not shown,
several feet of 4"x 8" I beam for aprons and the top main frame support.
1 3/8" solid steel weight lifting bar and end pieces, thought this could be used for the main press shaft
1 1/2" bed frame C channel - a bit light but planning on using it for the uprights feet
1 BIG hydraulic jack- the others i have are nowhere near 20 ton , but this 1 is at least that, - plan is to plumb it at some point for a gauge and then work out the pressure.?. Right now don't have any big jobs planned for this press but don't want to break the uprights due to over stressing them.
It was Cold when starting on this,
12* in the shop when I laid out the 7/8" holes for the pins and scribed the lines to split the 4x4 in two.
Had warmed up to 26 when the hole drilling was done- Man drilling 32 holes in a row by hand is a work out
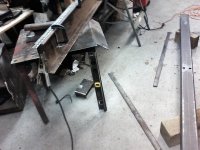
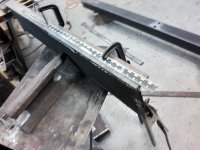
I was a bit concerned about firing up the plasma on my 3 in 1 machine in temps this low, but wanted to get going and thought that it might help to turn it on and let it idle for a couple minutes and then set the amps to just above minimum and lightly gouge a couple inches on the scribe line and warm the mosfets up a little bit before cranking it up to cut so that is what i did
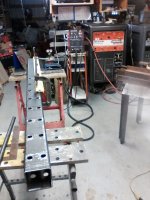
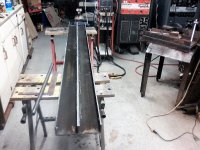
Next cut the bed frame rails and drilled holes in the uprights.
Welded the 2 trimmed 4 x 8 C channel together to form the top press piece with a void in the middle for the jack retract springs. Used 1/8 6011 and did my best to get full penetration in the gap between the 2 top plates added a piece of trimmed channel for where the jack seats on the top frame used 1/8 7018 for those welds.
Squared it up as much as I could ( sure would be nice to have a steel build table)
and welded the uprights to the center piece with more 1/8 7018- also added the (feet) thought i took some pictures but can't find them.
Here's the basic frame standing
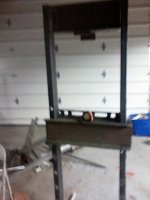
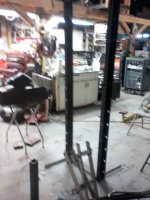
more to follow