Sodo
Elite Member
- Joined
- Apr 21, 2012
- Messages
- 3,212
- Location
- Cascade Mtns of WA state
- Tractor
- Kubota B-series & Mini Excavator
This is excerpted from a thread that got outta control, and closed.
Plate beveled at 60deg because everybody knows a 120v MIG can't melt far into a butt weld on 3/8" steel.
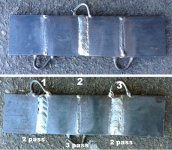
======= mostly a re-post =====================
This is Weld#2, the middle weld.
Root weld. (1/4" bolt is to show scale)

Third pass

Bent 90deg

Weld#2, it was very strong, had to reef on that 20T press to bend it to the 90-ish deg as shown.
But even though weld #2 was not 100%, it was firkin' strong (would not let trailer parts loose on the highway :laughing::laughing::laughing: )
Today I cut 'coupons' (sort of) so it would be easier to bend them with the 20Ton press. And busted them too. Will post those pics later as time allows.
This was kinda fun, even if rushed for time.
Plate beveled at 60deg because everybody knows a 120v MIG can't melt far into a butt weld on 3/8" steel.
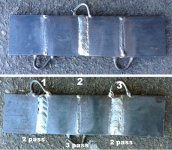
======= mostly a re-post =====================
This is Weld#2, the middle weld.
Root weld. (1/4" bolt is to show scale)

Third pass

Bent 90deg

Weld#2, it was very strong, had to reef on that 20T press to bend it to the 90-ish deg as shown.
But even though weld #2 was not 100%, it was firkin' strong (would not let trailer parts loose on the highway :laughing::laughing::laughing: )
Today I cut 'coupons' (sort of) so it would be easier to bend them with the 20Ton press. And busted them too. Will post those pics later as time allows.
This was kinda fun, even if rushed for time.
Last edited: