dieselfuelonly
Gold Member
Hi everyone, hopefully someone here can guide me in the right direction. My attachment plate and pin are badly worn, the previous owner greased everything, but apparently forgot about this area. The hole in the attachment plate almost became a little "egg shaped' from being beat on by the pin.
Anyway, I've got a new pin and two bushings from my Bobcat dealer. The bushings are supposed to be welded on.
And thats as much as I know. I don't know if its the kind of thing I can install myself, or if I'm gonna have to take it somewhere. If someone knows how this is done and can guide me, then from there I can figure out if its a project I can tackle or if I need to find someone else to do the work.
Hopefully everything makes sense in the pictures.
Anyway, I've got a new pin and two bushings from my Bobcat dealer. The bushings are supposed to be welded on.
And thats as much as I know. I don't know if its the kind of thing I can install myself, or if I'm gonna have to take it somewhere. If someone knows how this is done and can guide me, then from there I can figure out if its a project I can tackle or if I need to find someone else to do the work.
Hopefully everything makes sense in the pictures.

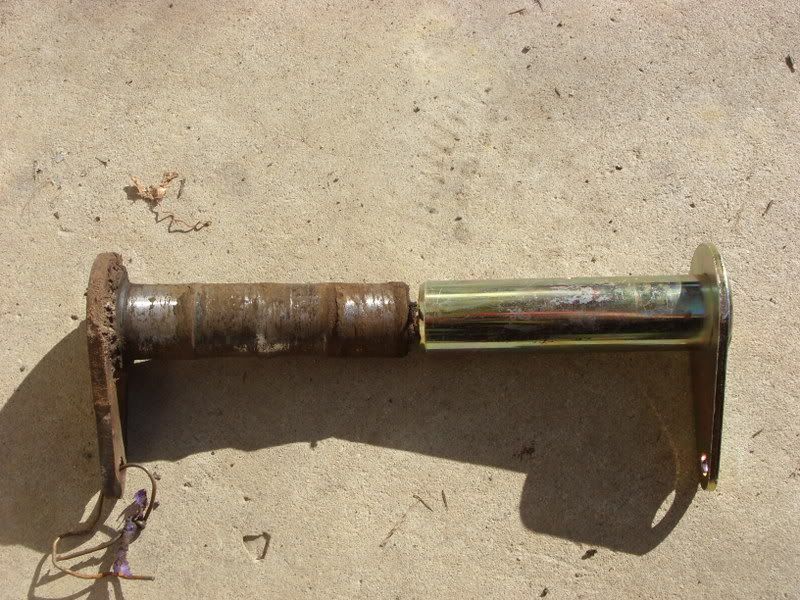
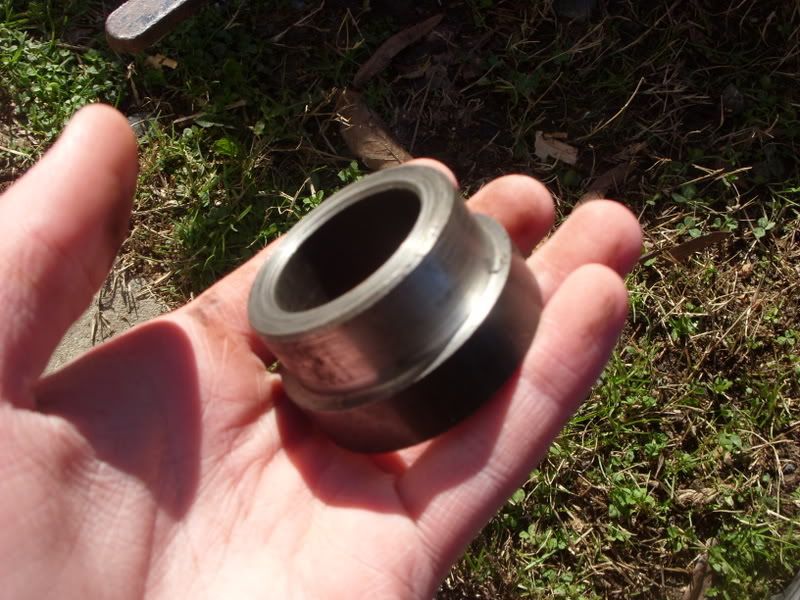
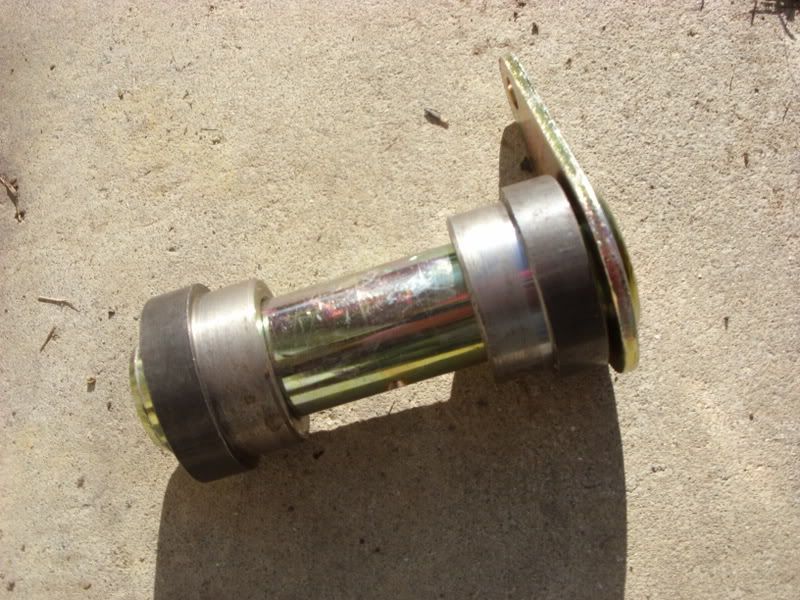