mide00532
New member
- Joined
- Jul 15, 2016
- Messages
- 4
- Location
- saint john
- Tractor
- Kubota B2320 HST - 48" Fel, 64" Snow Blower, 60" Mower Deck, 66" Land Pride Box Blade, Pallet Forks
Hi guys
Its my first time posting to this forum so if I break "write up rules" or something just let me know..
I wanted to initially buy some metal forks for just moving pallets of wood, tree limbs that get cut down etc, but soon realised that the quick attach for the 2320 (doesnt come stock) weighs about 300 pounds + costs 800-1000$, and the forks weigh about 150 pounds + cost 500$ish, together they put a big dent in this tractors 775 lb lifting capacity, after considering some clamp on forks i had decided against it because we would eventually bend the bucket lifting something thats too heavy.
running out of options and working on a budget (20 year old student) I decided to just make some out of wood as my dad owns a high end wood shop. I had originally been sent to a job site to tear down some hoarding that was keeping a door dry for paint, because it was covered in caulking and random paint colors it was considered garbage but I decided it would be good enough for me, I wish I would have started taking pictures before i did so i could do a better write up but I had originally thought this would be a few hours of work not day after day of modifying it to make it work.
All measurements included are retaliative to my bucket, any measurements you use will have to be to your bucket size, this is just a guide and will work the same if scaled up or down. I had a nice write up done but deleted it and decided to try and use more pictures than words
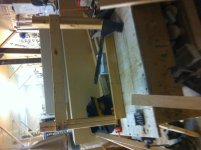
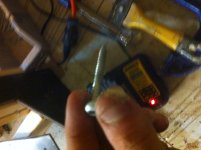
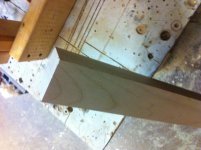
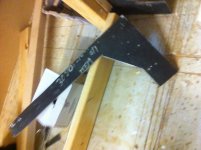
These four pictures are the only real pictures i have of assembling it, the frame itself is basically just a square with two pieces on the side to hold the forks down, i had intentionally left the sides about 18" higher than the bucket height so when your working with the forks you can see where the outside of your forks are instead of guessing.
I also didnt plan on adding cross bracing to help support the forks from moving side to side as i was only thinking about the forward and backward movement of the forks, after having it assembled i realised it was absolutely necessary to have cross pieces holding the forks in place or if you angle the tractor with the bucket low the forks will just snap off like a twig.
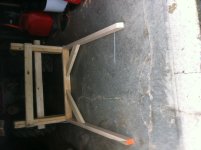
The last modification i had made before deeming them "ready" was adding a back support bar to avoid bending the bucket, its hard to explain but hopefully easy to see in the picture below that the bar in the back helps distribute the force over the entire top of the bucket when a load is put on the end of the forks, the forks will naturally want to go down, in turn pushing the frame of the forks up and this was an essential part to not having them come flying out of my bucket mid-load.
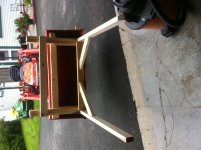
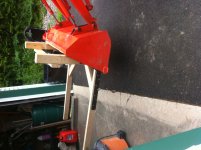

And without more babbling, some pictures of them actually lifting things - the pictures with the firewood pallets were overloading the tractor at one point so these forks can lift more than the tractor can lift. the trailer is just a little four wheeler trailer that i use to fill up plant pots with dirt and bring to the garden (can patch the tires by just lifting with the forks instead of jacks now) and the tree branches were from a 20 foot apple tree limb that rotted and collapsed on the lawn one night,
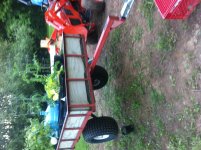
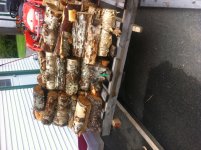
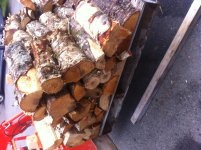
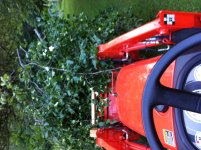

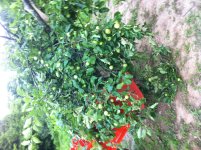
Now... was it worth it ?
At first i had mentioned quick attach - 300 pounds + 800-1000$ and the forks - 150 pounds + 500$ish, - so going with metal forks would have costed me roughly 1500$ and 450 / 775 lb lifting capacity - (at 4ft off the pivot point it would be even worse) but in the end I would have ended up with a brand new kubota quick attach with a set of OHSA forks - so for me it simply isnt viable to pay 1500$ to lift 300 lb loads.
For the wooden forks - my materials + price - this will be retail price - my total cost to make the forks were less than 40$ because I had everything I needed except 3 1/2 inch screws and I had to pay for gas back and forth to the shop like 5 times
1) roughly 5 spruce 2x4 - 10$ at hardware store
2) 1 board of maple (or 2 smaller sticks could be cheaper) - 1 board = 30$ or you could find 2 scrap sticks at a shop for 10$ if they cant make anything with it
3) pieces of metal - really not sure how much that would cost but i assume most people would go to a scrap yard or a friends house for some left overs - ill say $20 for the metal if you pay retail but i would check scrap yards before paying retail.
4) Screws - if you have to go buy all the screws 5-10$ (i had to buy 3 1/2 inch screws but got 500 on sale for 20$ to keep at the shop) - I would use outdoor screws but if its stored inside that helps.
5) PL - I used PL because i had access to it, I would highly recommend it but most binding adhesives will work. - maybe 15$
and thats about it for materials.. as for the tools i needed - chop saws, drill press (with metal bits for drilling screws holes) - caulking guns, table saws, drills etc so make sure you have the resources if you plan on making forks that will last.
after adding up the expenses i realised that i spent more on gas going back and forth between the shop than i did on the actual materials.
Grand total for metal forks - 450 lbs and 1500$
Grand total for wooden forks - roughly 60-75 lbs and 40$ counting gas - for a person to go out and buy all the materials It would be no more than $100 -
Again as ive said before, its my first time posting to this forum so if I broke a write up policy just tell me and I will change it.. im only 20 but I had the assistance of another forum member from here who is an exceptional builder to give me bits and pieces of advice along the way - its not the best but hopefully helps someone with a compact tractor..
Would love to see what other people have done for wooden forks because I still dont know what these are rated for, all I know is they can lift over 700 lbs and would love to build a set just to see much force it takes to break them .
Its my first time posting to this forum so if I break "write up rules" or something just let me know..
I wanted to initially buy some metal forks for just moving pallets of wood, tree limbs that get cut down etc, but soon realised that the quick attach for the 2320 (doesnt come stock) weighs about 300 pounds + costs 800-1000$, and the forks weigh about 150 pounds + cost 500$ish, together they put a big dent in this tractors 775 lb lifting capacity, after considering some clamp on forks i had decided against it because we would eventually bend the bucket lifting something thats too heavy.
running out of options and working on a budget (20 year old student) I decided to just make some out of wood as my dad owns a high end wood shop. I had originally been sent to a job site to tear down some hoarding that was keeping a door dry for paint, because it was covered in caulking and random paint colors it was considered garbage but I decided it would be good enough for me, I wish I would have started taking pictures before i did so i could do a better write up but I had originally thought this would be a few hours of work not day after day of modifying it to make it work.
All measurements included are retaliative to my bucket, any measurements you use will have to be to your bucket size, this is just a guide and will work the same if scaled up or down. I had a nice write up done but deleted it and decided to try and use more pictures than words
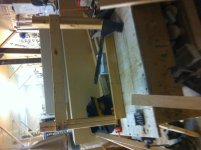
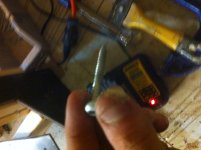
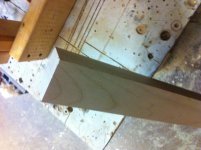
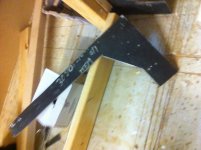
These four pictures are the only real pictures i have of assembling it, the frame itself is basically just a square with two pieces on the side to hold the forks down, i had intentionally left the sides about 18" higher than the bucket height so when your working with the forks you can see where the outside of your forks are instead of guessing.
I also didnt plan on adding cross bracing to help support the forks from moving side to side as i was only thinking about the forward and backward movement of the forks, after having it assembled i realised it was absolutely necessary to have cross pieces holding the forks in place or if you angle the tractor with the bucket low the forks will just snap off like a twig.
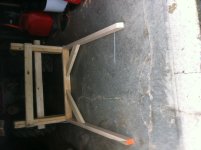
The last modification i had made before deeming them "ready" was adding a back support bar to avoid bending the bucket, its hard to explain but hopefully easy to see in the picture below that the bar in the back helps distribute the force over the entire top of the bucket when a load is put on the end of the forks, the forks will naturally want to go down, in turn pushing the frame of the forks up and this was an essential part to not having them come flying out of my bucket mid-load.
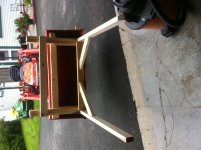
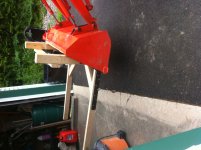

And without more babbling, some pictures of them actually lifting things - the pictures with the firewood pallets were overloading the tractor at one point so these forks can lift more than the tractor can lift. the trailer is just a little four wheeler trailer that i use to fill up plant pots with dirt and bring to the garden (can patch the tires by just lifting with the forks instead of jacks now) and the tree branches were from a 20 foot apple tree limb that rotted and collapsed on the lawn one night,
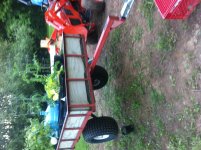
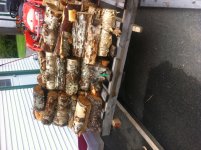
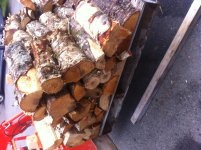
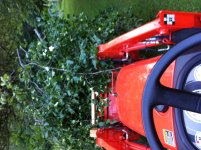

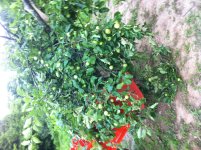
Now... was it worth it ?
At first i had mentioned quick attach - 300 pounds + 800-1000$ and the forks - 150 pounds + 500$ish, - so going with metal forks would have costed me roughly 1500$ and 450 / 775 lb lifting capacity - (at 4ft off the pivot point it would be even worse) but in the end I would have ended up with a brand new kubota quick attach with a set of OHSA forks - so for me it simply isnt viable to pay 1500$ to lift 300 lb loads.
For the wooden forks - my materials + price - this will be retail price - my total cost to make the forks were less than 40$ because I had everything I needed except 3 1/2 inch screws and I had to pay for gas back and forth to the shop like 5 times
1) roughly 5 spruce 2x4 - 10$ at hardware store
2) 1 board of maple (or 2 smaller sticks could be cheaper) - 1 board = 30$ or you could find 2 scrap sticks at a shop for 10$ if they cant make anything with it
3) pieces of metal - really not sure how much that would cost but i assume most people would go to a scrap yard or a friends house for some left overs - ill say $20 for the metal if you pay retail but i would check scrap yards before paying retail.
4) Screws - if you have to go buy all the screws 5-10$ (i had to buy 3 1/2 inch screws but got 500 on sale for 20$ to keep at the shop) - I would use outdoor screws but if its stored inside that helps.
5) PL - I used PL because i had access to it, I would highly recommend it but most binding adhesives will work. - maybe 15$
and thats about it for materials.. as for the tools i needed - chop saws, drill press (with metal bits for drilling screws holes) - caulking guns, table saws, drills etc so make sure you have the resources if you plan on making forks that will last.
after adding up the expenses i realised that i spent more on gas going back and forth between the shop than i did on the actual materials.
Grand total for metal forks - 450 lbs and 1500$
Grand total for wooden forks - roughly 60-75 lbs and 40$ counting gas - for a person to go out and buy all the materials It would be no more than $100 -
Again as ive said before, its my first time posting to this forum so if I broke a write up policy just tell me and I will change it.. im only 20 but I had the assistance of another forum member from here who is an exceptional builder to give me bits and pieces of advice along the way - its not the best but hopefully helps someone with a compact tractor..
Would love to see what other people have done for wooden forks because I still dont know what these are rated for, all I know is they can lift over 700 lbs and would love to build a set just to see much force it takes to break them .