texasranger556
Platinum Member
One of the projects on my (very long) list is a 3 point power rake for behind my JD 4400. Reasonably priced used ones are few and far between, and anything less than $2k looks like it would take a fair bit of work to make usable again...missing guards, missing teeth, trashed bearings, etc. New is out of the question, I just can't see how these things sell for $7000. My local rental yard hasn't heard of one. Might be able to find one at a dealer farther away, but I generally don't like renting anyway. My planned use include re-doing our 1 acre yard that has lots of dips and bumps that need to be leveled out. Lots of roots, but no rocks. We also live along a 1/4 mile private gravel drive that I would love to power rake out the pot holes rather than throwing several tons of crusher run at it each year.
I have a 5' chunk of 6" round steel which seems perfect for the drum (attached). Not sure the thickness since it has ends on it, but guessing about 250 lbs. Question is what to use for teeth. Commercial rakes use carbide, but with ~150 teeth at $10/per that is a bit too expensive and I only plan to use this thing about 10 hours per year, probably less.
Alternate ideas:
1) Grade 8 bolts. Weld 1/2" nuts to the drum, then thread in 1/2" bolts with lock washers or a second nut to take up any gap. The bolt length would be between 3/4-1". The head of the bolt would take most of the wear and could be unscrewed and replaced if necessary. Cost through mcmaster carr is $90 for 150 bolts plus $25 for nuts. Moving up to 5/8" is $135 and $50 for bolts and nuts.
2) Hand cut steel teeth. I have some old cutting edge that I could plasma cut into teeth and weld on. Probably only enough for 50-60 teeth so would have to buy additional material. Perhaps $200 for material, plus plasma consumables for cutting it to size.
3) Buy laser or plasma cut teeth. I don't know what this would cost and what type of material to ask for. Saves the tedious task of cutting the teeth by hand, but it would likely cost at least triple the other options.
I'm leaning toward option 1 because it is the cheapest and fairly simple. Question is how long would they last before needing replaced? Would I have to worry about the bolts shearing off? My intuition is the welds would likely break first.
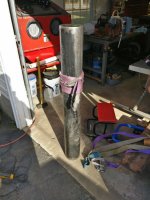
I have a 5' chunk of 6" round steel which seems perfect for the drum (attached). Not sure the thickness since it has ends on it, but guessing about 250 lbs. Question is what to use for teeth. Commercial rakes use carbide, but with ~150 teeth at $10/per that is a bit too expensive and I only plan to use this thing about 10 hours per year, probably less.
Alternate ideas:
1) Grade 8 bolts. Weld 1/2" nuts to the drum, then thread in 1/2" bolts with lock washers or a second nut to take up any gap. The bolt length would be between 3/4-1". The head of the bolt would take most of the wear and could be unscrewed and replaced if necessary. Cost through mcmaster carr is $90 for 150 bolts plus $25 for nuts. Moving up to 5/8" is $135 and $50 for bolts and nuts.
2) Hand cut steel teeth. I have some old cutting edge that I could plasma cut into teeth and weld on. Probably only enough for 50-60 teeth so would have to buy additional material. Perhaps $200 for material, plus plasma consumables for cutting it to size.
3) Buy laser or plasma cut teeth. I don't know what this would cost and what type of material to ask for. Saves the tedious task of cutting the teeth by hand, but it would likely cost at least triple the other options.
I'm leaning toward option 1 because it is the cheapest and fairly simple. Question is how long would they last before needing replaced? Would I have to worry about the bolts shearing off? My intuition is the welds would likely break first.
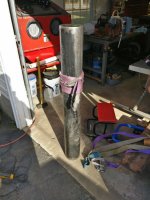