Shield Arc
Super Member
I really had my doubts that this was going to work. Lincoln's L-56 .035 inch wire on 1/2 inch thick material. I cut the bevels on the coupons at 37 1/2 degrees. I ran this at 18-volts, 198 wire speed, 125-amps, with 20 cfh of C/25 gas. I know a lot of charts say you can use .035 wire on 1/2 inch plate, but I didn't think it would work. Years ago one of the best weldors I ever had the pleasure of working with spliced some 3/4 inch thick plate using .035 wire, mainly because he was too lazy to change wires. When the plates were tested they failed!
These coupons were side bends, someone told me once a side bend test is harder to pass than a face and root bend. I don't know if that's true or not.


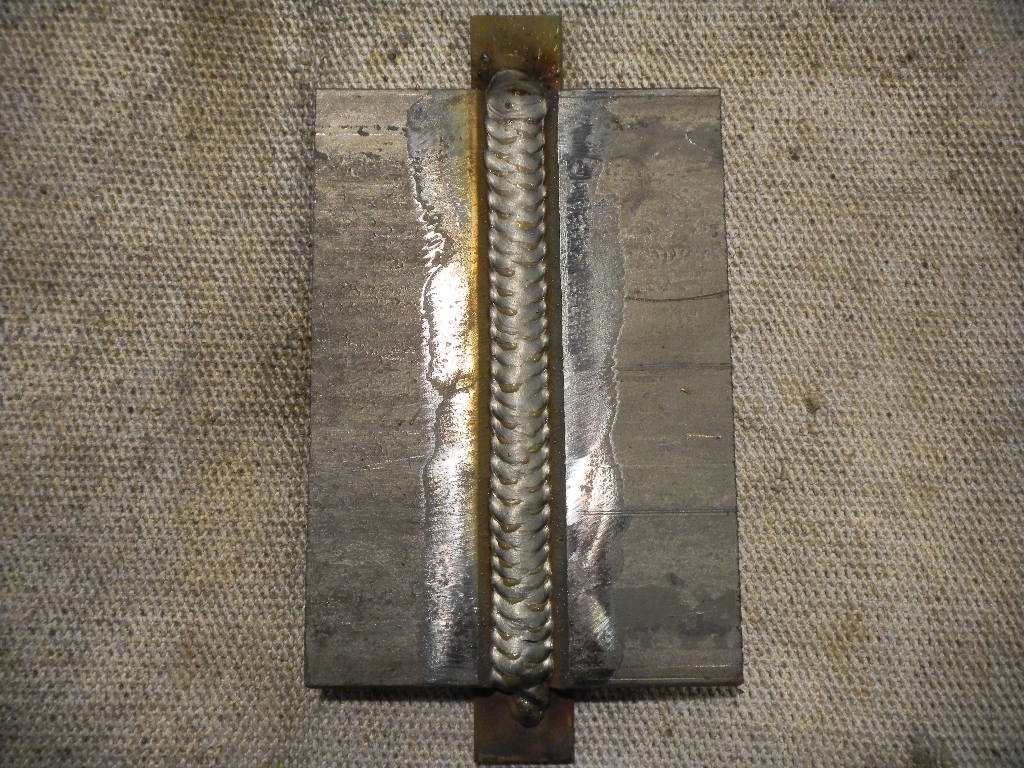






No visible flaws.


These coupons were side bends, someone told me once a side bend test is harder to pass than a face and root bend. I don't know if that's true or not.


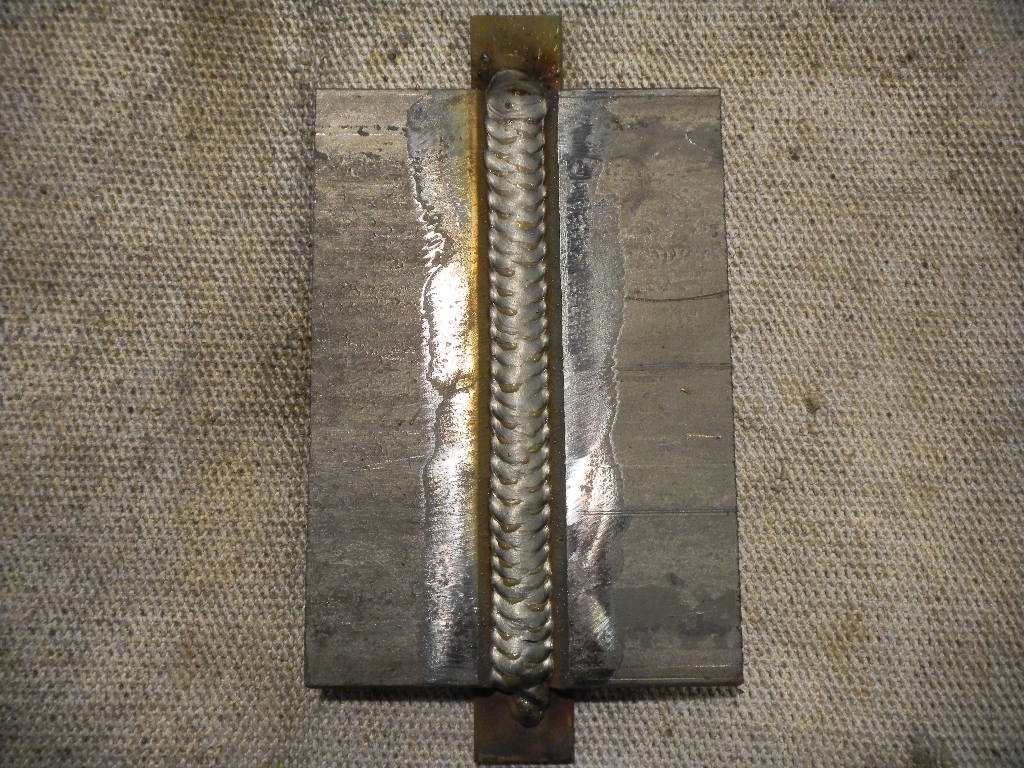






No visible flaws.

