Renze
Elite Member
I finished my outdoor stove last week. My friend used one of these brake drums as a simple fire pit, but it was too heavy to pull around in a town backyard. I picked it up, and found the other one also in a farmyard of another friend.
The problem with these things is that you can hardly weld them, so everything had to be bolted. I ordered a top cover from half inch steel, with the 10 holes on a 335mm circle (DIN standard for truck wheels) cut into them. Because i had to stuff both the chimney and the loading hatch in that top sheet, i made some cuts into the side, then gave the partially cut piece a blow with a hammer, because i could not grind it loose and then reweld the grinder slots. It broke clean off, no sweat at all.
For the bottom side, it needs to allow air to get in, but that would mean ash would drop out. Cleaning ash through the top hatch would be a pain anyways, so i decided to go full circle and make an ash drawer underneath in a separate chamber, welded from 8mm steel (5/16") and with a half inch fire grate above it.
the drums are stacked together, with a piece of flatbar bent into a circle over the perimeter of the drum, then dropped into the slot in the side, where normally the dirt shield of the axle runs. This prevents them from sliding and gives a good enough seal.
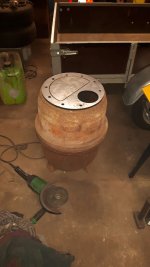
The hatch is a quarter inch bigger radius than the brake drum inner flange diameter, so the hatch lies on top of this edge, on the other side i welded a piece of flatbar under the hatch to seal it.
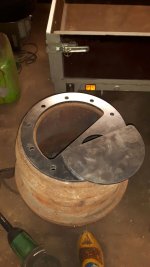
Then you see the ash grate, i used 3/4" slots with two interruptions, under which i welded an extra flatbar half inch by one inch, for added stability when the metal gets hot.
Ash tray is made of 4mm (5/32) and front end is made of 6mm (5/16)
I welded guide rails from another few pieces of scrap flatbar
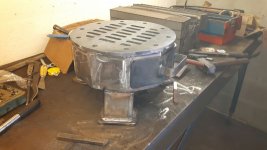
The ash tray goes underneath the grate and is also used to control combustion air. (along with four 3/4" holes in the bottom, both for drainage as well as to draw air in)
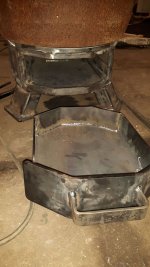
The top hatch, i made hinges also from flatbar, screwed an M10 bolt through it, clamped it with an M10 nut, so i get cantilevered pins that are removeable. All you have to do is hold that M10 nut in place whilst screwing the bolt in place, because the way the hinge strips are welded, they can not move to the side all that much.

I put on a piece of wood on a bolt as handle, but its still too hot to touch. Will put it on a longer piece of metal, further away from the heat source.
The chimney is a piece of 5 inch pipe.
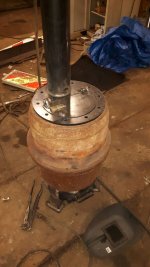
The rain cap was an old chromed wheel cap from a trailer. Will wrap some wire mesh around the exit area beneath it, to catch fly fire. Cant take no risk next to a reed roof during dry summers...
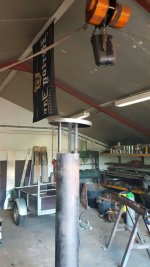
My neighbour is an industrial painter who gets to touch up industrial installations and buildings. he loves his work, so i gladly let him do the painting. Paint came in rattle cans, and is resistant up to 800 degrees. He did a nice job.
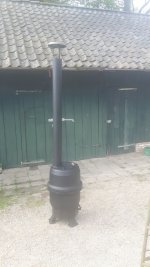
Then you see a picture of the lid open, normal burning. The cast iron radiates a lot of heat, even when there is a slight wind: The beauty of cast iron is that it doesnt directly transfer heat to the air that much, but it radiates the heat: less of it is carried away by the wind, the people sitting close to it dont get scorched, and the people behind them still get their share of heat.
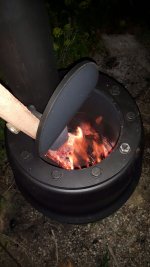
Last photo shows what happens when you throw a cardboard box in it: It lit up the night with a cool jet flame
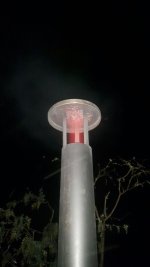
The problem with these things is that you can hardly weld them, so everything had to be bolted. I ordered a top cover from half inch steel, with the 10 holes on a 335mm circle (DIN standard for truck wheels) cut into them. Because i had to stuff both the chimney and the loading hatch in that top sheet, i made some cuts into the side, then gave the partially cut piece a blow with a hammer, because i could not grind it loose and then reweld the grinder slots. It broke clean off, no sweat at all.
For the bottom side, it needs to allow air to get in, but that would mean ash would drop out. Cleaning ash through the top hatch would be a pain anyways, so i decided to go full circle and make an ash drawer underneath in a separate chamber, welded from 8mm steel (5/16") and with a half inch fire grate above it.
the drums are stacked together, with a piece of flatbar bent into a circle over the perimeter of the drum, then dropped into the slot in the side, where normally the dirt shield of the axle runs. This prevents them from sliding and gives a good enough seal.
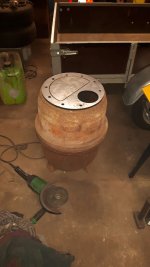
The hatch is a quarter inch bigger radius than the brake drum inner flange diameter, so the hatch lies on top of this edge, on the other side i welded a piece of flatbar under the hatch to seal it.
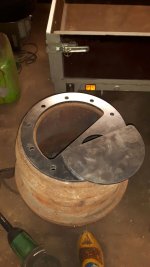
Then you see the ash grate, i used 3/4" slots with two interruptions, under which i welded an extra flatbar half inch by one inch, for added stability when the metal gets hot.
Ash tray is made of 4mm (5/32) and front end is made of 6mm (5/16)
I welded guide rails from another few pieces of scrap flatbar
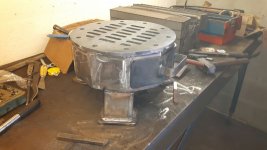
The ash tray goes underneath the grate and is also used to control combustion air. (along with four 3/4" holes in the bottom, both for drainage as well as to draw air in)
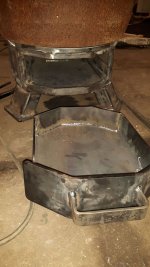
The top hatch, i made hinges also from flatbar, screwed an M10 bolt through it, clamped it with an M10 nut, so i get cantilevered pins that are removeable. All you have to do is hold that M10 nut in place whilst screwing the bolt in place, because the way the hinge strips are welded, they can not move to the side all that much.

I put on a piece of wood on a bolt as handle, but its still too hot to touch. Will put it on a longer piece of metal, further away from the heat source.
The chimney is a piece of 5 inch pipe.
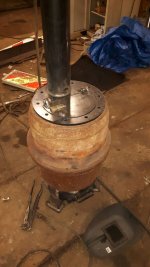
The rain cap was an old chromed wheel cap from a trailer. Will wrap some wire mesh around the exit area beneath it, to catch fly fire. Cant take no risk next to a reed roof during dry summers...
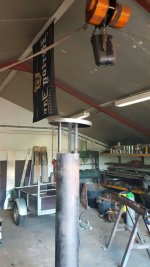
My neighbour is an industrial painter who gets to touch up industrial installations and buildings. he loves his work, so i gladly let him do the painting. Paint came in rattle cans, and is resistant up to 800 degrees. He did a nice job.
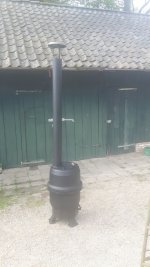
Then you see a picture of the lid open, normal burning. The cast iron radiates a lot of heat, even when there is a slight wind: The beauty of cast iron is that it doesnt directly transfer heat to the air that much, but it radiates the heat: less of it is carried away by the wind, the people sitting close to it dont get scorched, and the people behind them still get their share of heat.
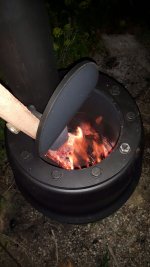
Last photo shows what happens when you throw a cardboard box in it: It lit up the night with a cool jet flame
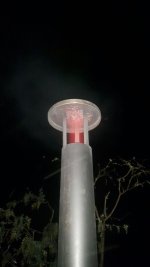
Last edited: