joshuabardwell
Elite Member
My garden cart's steering rack broke. Now I'm fixing it.
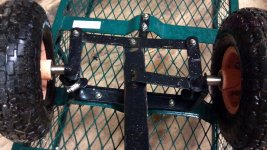
The broken rack.
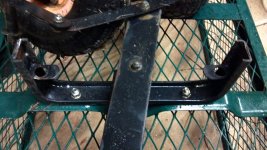
Used a cutoff wheel in an angle grinder to cut out the (tiny) welds holding the original piece in.
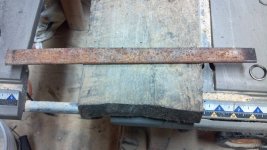
I didn't have a piece of 1/8" flat stock handy, so I cut one out of some 3/16" stock that I had laying around. I used a Diablo metal cutting blade. It is awesome, but I don't recommend making rip cuts out of flat stock with one. It's too hard to keep them straight, and it wears the blade out really fast.
This first piece that I cut, I failed to account for the kerf of the blade, and it was too narrow to cut the holes it was going to need in order to have the wheel posts pass through it. So I cut another one. My blade wasn't brand new, but that last rip cut finished it off.
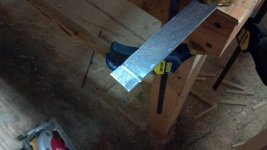
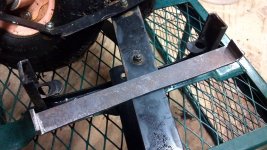
The original piece was actually bent to ninety degrees at the end. I'm not sure why, since it was only welded at the corner, but just to be safe, I replicated the piece. At the very least, the ears will help hold the piece in place with friction while I'm welding it. I used a grinder wheel to cut a gap and then bent it over with pliers. I considered welding a bead on the inside of the corner, but decided not to. For one thing, the remaining metal holding the corner together is at least as thick as the original piece was. For another thing, the new piece is even thicker than the original piece was, so it should be plenty strong. Finally, it's raining, so I didn't want to weld, so if I waited to weld it up, I would have to stop the whole project.
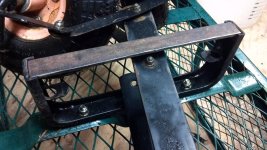
Pretty good fit! Next, I drilled the holes. I used a hole saw in a drill press to make the holes for the wheel posts. One thing I have learned about using hole saws with metal is that I should pre-drill the pilot hole using a regular drill bit before going at it with the hole saw. Multiple times now, what has happened is that I'm pushing hard on the hole saw's pilot bit and when it breaks through, I gouge the hole saw into the metal, bending the pilot bit and near twisting my own wrist off. You would think I would learn after the first time, but I'm a slow learner sometimes.
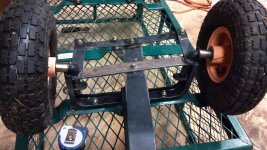
Dry fitup before welding. It's not 100% perfect, but I think it'll work. I'm not sure why, but with the center hole dead center on the piece, it actually doesn't line up right with the handle. Maybe the handle got tweaked somehow, I don't know. The original piece was centered, for sure. The other thing is, I didn't have the exact right size hole saw for the wheel posts. The original holes were 5/8". I have a 1/2" bit and a 3/4" hole saw. So I used the hole saw because I didn't relish the idea of filing out the 1/2" holes the extra 1/8". The wheels will have a little extra slop in them, but only a little more slop than they had to begin with, and it'll still be way stronger than it was when it was broken and held together with a hose clamp.
While I was at it, I noticed that the rear bar of the rack was also pretty bent up, probably from rolling the cart around with the broken front bar, so I took that piece that I accidentally cut too narrow, drilled three holes in it, and used it to replace the rear bar.
It's raining out right now, so no welding. Once we get a dry day, I'll take it over and weld it up. Just two small beads and good to go!
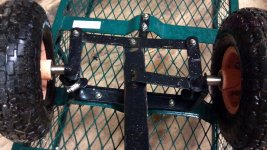
The broken rack.
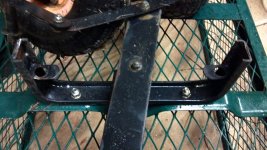
Used a cutoff wheel in an angle grinder to cut out the (tiny) welds holding the original piece in.
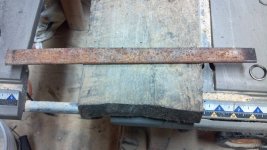
I didn't have a piece of 1/8" flat stock handy, so I cut one out of some 3/16" stock that I had laying around. I used a Diablo metal cutting blade. It is awesome, but I don't recommend making rip cuts out of flat stock with one. It's too hard to keep them straight, and it wears the blade out really fast.
This first piece that I cut, I failed to account for the kerf of the blade, and it was too narrow to cut the holes it was going to need in order to have the wheel posts pass through it. So I cut another one. My blade wasn't brand new, but that last rip cut finished it off.
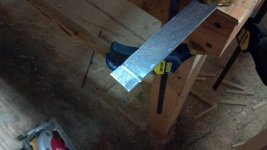
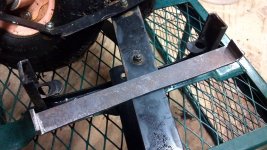
The original piece was actually bent to ninety degrees at the end. I'm not sure why, since it was only welded at the corner, but just to be safe, I replicated the piece. At the very least, the ears will help hold the piece in place with friction while I'm welding it. I used a grinder wheel to cut a gap and then bent it over with pliers. I considered welding a bead on the inside of the corner, but decided not to. For one thing, the remaining metal holding the corner together is at least as thick as the original piece was. For another thing, the new piece is even thicker than the original piece was, so it should be plenty strong. Finally, it's raining, so I didn't want to weld, so if I waited to weld it up, I would have to stop the whole project.
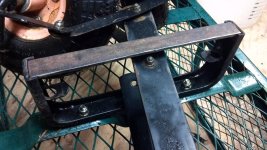
Pretty good fit! Next, I drilled the holes. I used a hole saw in a drill press to make the holes for the wheel posts. One thing I have learned about using hole saws with metal is that I should pre-drill the pilot hole using a regular drill bit before going at it with the hole saw. Multiple times now, what has happened is that I'm pushing hard on the hole saw's pilot bit and when it breaks through, I gouge the hole saw into the metal, bending the pilot bit and near twisting my own wrist off. You would think I would learn after the first time, but I'm a slow learner sometimes.
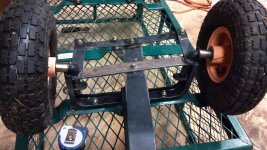
Dry fitup before welding. It's not 100% perfect, but I think it'll work. I'm not sure why, but with the center hole dead center on the piece, it actually doesn't line up right with the handle. Maybe the handle got tweaked somehow, I don't know. The original piece was centered, for sure. The other thing is, I didn't have the exact right size hole saw for the wheel posts. The original holes were 5/8". I have a 1/2" bit and a 3/4" hole saw. So I used the hole saw because I didn't relish the idea of filing out the 1/2" holes the extra 1/8". The wheels will have a little extra slop in them, but only a little more slop than they had to begin with, and it'll still be way stronger than it was when it was broken and held together with a hose clamp.
While I was at it, I noticed that the rear bar of the rack was also pretty bent up, probably from rolling the cart around with the broken front bar, so I took that piece that I accidentally cut too narrow, drilled three holes in it, and used it to replace the rear bar.
It's raining out right now, so no welding. Once we get a dry day, I'll take it over and weld it up. Just two small beads and good to go!
Last edited: