crazyal
Super Member
I debated if this belongs here or in the welding section but here goes. The wear bar on my Kubota snow blower needed replacing. For $80 (with new bolts, nuts, and tax) I figured it was a little pricey but an easy solution. I just ordered generic grade 5 plow bolts vs buying the much more expensive ones from Kubota so maybe this had an impact on the problem. The problem was the countersunk hole isn't deep enough and the head of the plow bolt is slightly above the surface of the steel. The square part of the hole is a lot deeper than that the bolt needs. I just used the drill press with a 3/4" countersink to fix the problem.
This has me asking myself why not make it myself. I quickly looked into it but it seamed like a punch was an expensive option and the wobbly drill bit would require work and if not accurate enough the square hole wouldn't keep the bolt from spinning so I passed and just bought the part. It's just 1 1/2" x 3/8" mild steel. But now that I'm deepening the countersink holes anyway maybe I should rethink giving up on the idea of making my own.
The bolts are 3/8". I'm thinking that drilling a 3/8" hole then finding a way to make it square would probably be easiest. But I would like to hear what others have done. Here's a before and after.
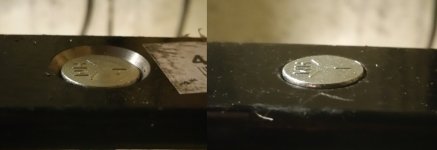
This has me asking myself why not make it myself. I quickly looked into it but it seamed like a punch was an expensive option and the wobbly drill bit would require work and if not accurate enough the square hole wouldn't keep the bolt from spinning so I passed and just bought the part. It's just 1 1/2" x 3/8" mild steel. But now that I'm deepening the countersink holes anyway maybe I should rethink giving up on the idea of making my own.
The bolts are 3/8". I'm thinking that drilling a 3/8" hole then finding a way to make it square would probably be easiest. But I would like to hear what others have done. Here's a before and after.
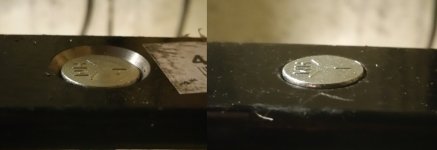