Hilbilly
Veteran Member
The pins and bushings in my 763 Bobtach were all badly worn and it was almost impossible to do any reasonable grading with it. I took it to a machine shop and was given a verbal estimate of $1800 just to bore out the 2 end pins and the ears. That didn't include any replacement parts just the boring. So a little research on the net and I found some home made methods for boring the ears. I also figured I would try making my own pins and bushings with the small metal lathe and a milling machine I recently purchased. It took considerably longer than expected but the whole thing was a learning experience and well worth the effort. I also discovered that machining is a LOT more complicated than it appears.
I didn't get pics of all the pins and bushings I made (should have but got busy and forgot). In total there were 4 pins and 7 bushings (including 2 temporary tapered alignment bushings).
I even did some heat treating for the first time.
Here are some pics:
1. Old and new tapered pins.
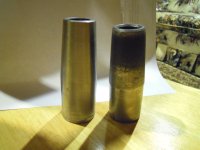
2. Internal threads on new pin.

3. Worn pin receiver that is oblong and tapered from front to back. Should be straight.

4. New bushing tapered to fit wear on receiver and straight in the middle.

5. New pin sitting in new bushing. Nice snug fit.

6. Getting the boring bar centered in the ears using tapered bushings.

7. All set up and ready to bore.
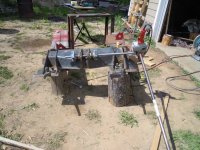
8. Boring bar cutter shown between the ears. This was pulled and pushed into the ears on each side.

9. Tilt cylinder on mill. Lots of time required to set it up. This bore wasn't even included in the $1800 quote.

10. Finished tilt cylinder bore.

I can't believe the difference this made. It's like a totally different machine. There is no slop in the tilt function of the bucket now and before this there was probably 4" to 6" of slop. Turned out better than expected. I'm very happy and I've learned some new skills, which I'm sure will come in handy in the not so distant future.
I didn't get pics of all the pins and bushings I made (should have but got busy and forgot). In total there were 4 pins and 7 bushings (including 2 temporary tapered alignment bushings).
I even did some heat treating for the first time.
Here are some pics:
1. Old and new tapered pins.
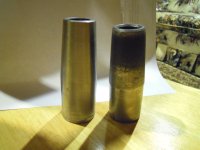
2. Internal threads on new pin.

3. Worn pin receiver that is oblong and tapered from front to back. Should be straight.

4. New bushing tapered to fit wear on receiver and straight in the middle.

5. New pin sitting in new bushing. Nice snug fit.

6. Getting the boring bar centered in the ears using tapered bushings.

7. All set up and ready to bore.
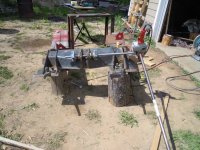
8. Boring bar cutter shown between the ears. This was pulled and pushed into the ears on each side.

9. Tilt cylinder on mill. Lots of time required to set it up. This bore wasn't even included in the $1800 quote.

10. Finished tilt cylinder bore.

I can't believe the difference this made. It's like a totally different machine. There is no slop in the tilt function of the bucket now and before this there was probably 4" to 6" of slop. Turned out better than expected. I'm very happy and I've learned some new skills, which I'm sure will come in handy in the not so distant future.