jimcolt
Gold Member
There are dozens of different manufacturers of plasma cutting systems around the world, with air plasma systems sized from 20 Amps to 400 amps. Prices will vary rather dramatically, cut thickness and speed ratings as well......and if it is important you can get almost any color you want! Reading the manufacturers shiny, multi color brochures when comparing plasma cutters and welders makes it clear that each is (of course) trying to convince us that theirs is the biggest, baddest, fastest plasma cutter on the planet. In reality, they all cut metal.....so how can we compare system to system with some meaningful information?
I get these kinds of questions daily on a variety of forums, and after 35 (close to 36!) years in the plasma cutting business I still try to answer each individual question along these lines based on the users actual needs. If all you ever cut is 10 gauge steel and thinner, then their certainly is no need for a 125 amp, 100% duty cycle air plasma cutting system. If you are a hobbiest that only works on your hot rod projects on weekends, with occasionally severencing an exhaust bracket....then maybe a low cost import plasma will fit your needs perfectly. If you are a job shop that needs to cut a variety of thicknesses, use the plasma with both hand torches and cnc machine torches and rely on tools like this for your income...then the choice often will be based somewhat differently than the above scenarios. Longer lasting, easier to use, reliability, versatile are words that come to mind.
So, while I plan on talking about different aspects of plasma cutters in a few different posts....things such as torch design (are they all the same?), consumable parts design (why do some systems use one nozzle/tip for the whole cutting range where others have multiple choices?), as well as power supply DC output characteristics.....today I just want to show a typical plasma cutter power supply specification sheet.....showing the design output capabilities of a typical system.
This can be boring stuff, but in reality with a plasma cutter (and welders as well) it is not simply the output amperage that provides the power that you will be cutting with....there are 30 amp plasma cutters that cut thicker and faster than many 40 amp cutters. Duty cycle may not be much of a concern for the occasional hobbiest, however anytime you put a plasma on a cnc machine expect higher on vs off times than typical with hand cutting applications. When you cut thicker....even at the same amperage...the duty cycle is affected, and when you cut on a hot day, same issue. If you want a plasma or a welder to be able to perform under tough conditions....a properly specified duty cycle is certainly critical.
Along the same lines.....when a manufacturer states duty cycle at say 60%, take a close look at the supplied specifications as duty cycle cannot be honestly stated unless there is an ambient temperature and a load voltage that the duty cycle is rated at. Often....the 60% may be real but only on a 70 degree day and only when cutting gauge thickness....on thicker materials and hot days the duty cycle can be as low as 10%....I have experienced this!
So, attached is a power supply spec sheet for a major manufacturers 45 amp plasma system, lets go over some of this:
Rated open circuit voltage: This is a safety spec. Under certain conditions, usually exposed torch wires or damaged torch handles..this voltage could be present and should be considered very dangerous. Higher open circuit voltages do not offer advantages, but can offer higher chance of dangerous shock. Generally older technology power supplies with older technology torches have higher open circuit voltages in order to make arc starting easier and more reliable.
Rated Output Current: This is the designed operating range of the plasma cutter. I will bring up the importance of having a range of amperage in a later post when talking about consumables and cut quality.
Rated Output Voltage This is the arc voltage that the duty cycle rating of the power supply is based on. Arc voltage and arc length are proportional, so to cut thicker material the arc gets longer, the voltage gets higher. On this particular manufacturers systems the rated voltage is always the voltage required to cut the advertised production thickness. Be careful when looking at this as many (yes even the major manufacturers) often use a lower "rated" arc voltage allowing them to publish a higher duty cycle number, when cutting the advertised production thickness the duty cycle in these cases will be somewhat lower.
Current or Amperage....and voltage are two distinctly different measures of cutting capability. Amperage is a fairly good indicator of the plasma cutters power, and can be set with a knob by the operator. Voltage with a plasma cutter is entirely dependent on the length of the cutting arc. If you multiply the maximum amperage x the rated voltage you will get the rated Wattage of the plasma system. Wattage is a true measure of the amount of power that a plasma cutting power supply can produce, when there also is a duty cycle and ambient temperature rating. All plasma power supplies can produce a higher voltage (than the rated voltage) and a higher Wattage output, but the power supply has to work harder, producing more internal heat, which will shorten the effective duty cycle.
Duty Cycle at 40C Most plasma cutters and welders (not all) use IEC standards for Industrial Equipment for rating the duty cycle based on a known ambient temperature of 40C, which is equivalent to 104 degrees F. If you cannot find this spec in the spec sheet or manual for a particular piece of equipment....you probably should not trust the ratings for duty cycle to be accurate. This is the actual testing temperature that duty cycle ratings are developed at in the design lab. The power supply is brought up to its ambient temp, then cutting is done at maximum current at a fixed arc voltage and the when components inside the power supply (normally transformers, switching devices, etc) reach their manufacturers maximum operating temp....you have reached duty cycle. Most manufacturers design in temperature sensors that will shut down the system when max temperature is reached, some do not.
On this system there are three different duty cycle calculations shown, the first is at the advertised 60% duty cycle rating for cutting the advertised production thickness of 1/2" steel, the second shows that if you still cut the 1/2" steel at 132 arc volts, but reduce the amperage (lower cut speed), that the duty cycle increases. The third shows at what amperage and voltage the power supply can achieve 100% duty cycle. It happens to occur at 32 amps x 132 volts or 4224 watts on a 104 degree day. At the rated 50% duty cycle is produces 5940 watts on a 104 degree day. All honest lab tested ratings.
In reality, if the manufacturers ratings are complete and honest....50% duty cycle is usually more than adequate for even busy hand held cutting applications. For mechanized cutting you should consider higher ratings. Achieving higher ratings often just means choosing a more powerful plasma cutter than you need and running it at lower than full output....which can get you to 100% duty.
Operating Temperature This manufacturer uses specifications listed by the worst case internal component manufacturer (discrete PC board components, transformers, switching devices, etc.) as the minimum and maximum operating temp. While the systems certainly will operate at temperatures that are lower and higher than the ones listed (I have personally exceeded specs on both ends of the spectrum!), it is possible that power supply output accuracy in terms of amperage, voltage, starting/stopping power ramps, etc) may be affected, which could affect cut quality and or torch performance.
Storage temperature This is self explanatory.
Power Factor This is an indication of the efficiency of a particular power supply design. It essentially means that (with a higher number) that more of the power from your shops electrical circuit is actually getting to the torch cutting process, as opposed to being turned into power supply heat. A lot of people are not aware of the efficiency of a well designed plasma cutter...it can be in the range of 90% efficient, wall power to cutting power. An industrial cutting laser system (for comparison) is only in the 15% to 20% efficiency range.
Input Voltage Indicates the different available voltages that the units will operate at, and the current (amperage) draw on the shop power system. As with all electrical equipment, higher input voltages will use less amperage, meaning electrical cords and wiring can be smaller and lower cost.
Gas Quality The system will perform with the best cut quality with gas purity (air in this case) that is clean, dry and oil free. Depending on your air system and / or the relative humidity of the region you are using your plasma system in.....will determine if any addition treatment (drying, filtering) of compressed air is necessary. The majority of plasma system users need no extra treatment, in fact I find one of the biggest causes of issues with air supplied to an air plasma is starvation.....a pressure drop to the inlet of the plasma created by too many filters!
Inlet gas flow and Pressure This info is necessary in order to determine the size of the plumbing, the size of the compressor that will be used for plasma cutting. With this manufacturer it is the maximum rating using the largest (highest amperage, nozzle size) set of consumables. Using lower powered consumable sets with a smaller nozzle orifice uses less air.
Hopefully others will jump in with similar specs, or at least lets get some dialogue going about the specs discussed here. If you are looking for best performance in terms of cut quality, cut speed and consumable life with plasma cutting it is important to have an understanding of these basic specs. There of course is a lot more regarding torches, air flow control, consumables and how when these components are designed together that can take full advantage of the laws of high temperature physics.
Jim Colt
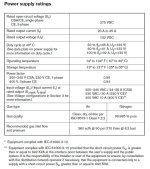
I get these kinds of questions daily on a variety of forums, and after 35 (close to 36!) years in the plasma cutting business I still try to answer each individual question along these lines based on the users actual needs. If all you ever cut is 10 gauge steel and thinner, then their certainly is no need for a 125 amp, 100% duty cycle air plasma cutting system. If you are a hobbiest that only works on your hot rod projects on weekends, with occasionally severencing an exhaust bracket....then maybe a low cost import plasma will fit your needs perfectly. If you are a job shop that needs to cut a variety of thicknesses, use the plasma with both hand torches and cnc machine torches and rely on tools like this for your income...then the choice often will be based somewhat differently than the above scenarios. Longer lasting, easier to use, reliability, versatile are words that come to mind.
So, while I plan on talking about different aspects of plasma cutters in a few different posts....things such as torch design (are they all the same?), consumable parts design (why do some systems use one nozzle/tip for the whole cutting range where others have multiple choices?), as well as power supply DC output characteristics.....today I just want to show a typical plasma cutter power supply specification sheet.....showing the design output capabilities of a typical system.
This can be boring stuff, but in reality with a plasma cutter (and welders as well) it is not simply the output amperage that provides the power that you will be cutting with....there are 30 amp plasma cutters that cut thicker and faster than many 40 amp cutters. Duty cycle may not be much of a concern for the occasional hobbiest, however anytime you put a plasma on a cnc machine expect higher on vs off times than typical with hand cutting applications. When you cut thicker....even at the same amperage...the duty cycle is affected, and when you cut on a hot day, same issue. If you want a plasma or a welder to be able to perform under tough conditions....a properly specified duty cycle is certainly critical.
Along the same lines.....when a manufacturer states duty cycle at say 60%, take a close look at the supplied specifications as duty cycle cannot be honestly stated unless there is an ambient temperature and a load voltage that the duty cycle is rated at. Often....the 60% may be real but only on a 70 degree day and only when cutting gauge thickness....on thicker materials and hot days the duty cycle can be as low as 10%....I have experienced this!
So, attached is a power supply spec sheet for a major manufacturers 45 amp plasma system, lets go over some of this:
Rated open circuit voltage: This is a safety spec. Under certain conditions, usually exposed torch wires or damaged torch handles..this voltage could be present and should be considered very dangerous. Higher open circuit voltages do not offer advantages, but can offer higher chance of dangerous shock. Generally older technology power supplies with older technology torches have higher open circuit voltages in order to make arc starting easier and more reliable.
Rated Output Current: This is the designed operating range of the plasma cutter. I will bring up the importance of having a range of amperage in a later post when talking about consumables and cut quality.
Rated Output Voltage This is the arc voltage that the duty cycle rating of the power supply is based on. Arc voltage and arc length are proportional, so to cut thicker material the arc gets longer, the voltage gets higher. On this particular manufacturers systems the rated voltage is always the voltage required to cut the advertised production thickness. Be careful when looking at this as many (yes even the major manufacturers) often use a lower "rated" arc voltage allowing them to publish a higher duty cycle number, when cutting the advertised production thickness the duty cycle in these cases will be somewhat lower.
Current or Amperage....and voltage are two distinctly different measures of cutting capability. Amperage is a fairly good indicator of the plasma cutters power, and can be set with a knob by the operator. Voltage with a plasma cutter is entirely dependent on the length of the cutting arc. If you multiply the maximum amperage x the rated voltage you will get the rated Wattage of the plasma system. Wattage is a true measure of the amount of power that a plasma cutting power supply can produce, when there also is a duty cycle and ambient temperature rating. All plasma power supplies can produce a higher voltage (than the rated voltage) and a higher Wattage output, but the power supply has to work harder, producing more internal heat, which will shorten the effective duty cycle.
Duty Cycle at 40C Most plasma cutters and welders (not all) use IEC standards for Industrial Equipment for rating the duty cycle based on a known ambient temperature of 40C, which is equivalent to 104 degrees F. If you cannot find this spec in the spec sheet or manual for a particular piece of equipment....you probably should not trust the ratings for duty cycle to be accurate. This is the actual testing temperature that duty cycle ratings are developed at in the design lab. The power supply is brought up to its ambient temp, then cutting is done at maximum current at a fixed arc voltage and the when components inside the power supply (normally transformers, switching devices, etc) reach their manufacturers maximum operating temp....you have reached duty cycle. Most manufacturers design in temperature sensors that will shut down the system when max temperature is reached, some do not.
On this system there are three different duty cycle calculations shown, the first is at the advertised 60% duty cycle rating for cutting the advertised production thickness of 1/2" steel, the second shows that if you still cut the 1/2" steel at 132 arc volts, but reduce the amperage (lower cut speed), that the duty cycle increases. The third shows at what amperage and voltage the power supply can achieve 100% duty cycle. It happens to occur at 32 amps x 132 volts or 4224 watts on a 104 degree day. At the rated 50% duty cycle is produces 5940 watts on a 104 degree day. All honest lab tested ratings.
In reality, if the manufacturers ratings are complete and honest....50% duty cycle is usually more than adequate for even busy hand held cutting applications. For mechanized cutting you should consider higher ratings. Achieving higher ratings often just means choosing a more powerful plasma cutter than you need and running it at lower than full output....which can get you to 100% duty.
Operating Temperature This manufacturer uses specifications listed by the worst case internal component manufacturer (discrete PC board components, transformers, switching devices, etc.) as the minimum and maximum operating temp. While the systems certainly will operate at temperatures that are lower and higher than the ones listed (I have personally exceeded specs on both ends of the spectrum!), it is possible that power supply output accuracy in terms of amperage, voltage, starting/stopping power ramps, etc) may be affected, which could affect cut quality and or torch performance.
Storage temperature This is self explanatory.
Power Factor This is an indication of the efficiency of a particular power supply design. It essentially means that (with a higher number) that more of the power from your shops electrical circuit is actually getting to the torch cutting process, as opposed to being turned into power supply heat. A lot of people are not aware of the efficiency of a well designed plasma cutter...it can be in the range of 90% efficient, wall power to cutting power. An industrial cutting laser system (for comparison) is only in the 15% to 20% efficiency range.
Input Voltage Indicates the different available voltages that the units will operate at, and the current (amperage) draw on the shop power system. As with all electrical equipment, higher input voltages will use less amperage, meaning electrical cords and wiring can be smaller and lower cost.
Gas Quality The system will perform with the best cut quality with gas purity (air in this case) that is clean, dry and oil free. Depending on your air system and / or the relative humidity of the region you are using your plasma system in.....will determine if any addition treatment (drying, filtering) of compressed air is necessary. The majority of plasma system users need no extra treatment, in fact I find one of the biggest causes of issues with air supplied to an air plasma is starvation.....a pressure drop to the inlet of the plasma created by too many filters!
Inlet gas flow and Pressure This info is necessary in order to determine the size of the plumbing, the size of the compressor that will be used for plasma cutting. With this manufacturer it is the maximum rating using the largest (highest amperage, nozzle size) set of consumables. Using lower powered consumable sets with a smaller nozzle orifice uses less air.
Hopefully others will jump in with similar specs, or at least lets get some dialogue going about the specs discussed here. If you are looking for best performance in terms of cut quality, cut speed and consumable life with plasma cutting it is important to have an understanding of these basic specs. There of course is a lot more regarding torches, air flow control, consumables and how when these components are designed together that can take full advantage of the laws of high temperature physics.
Jim Colt
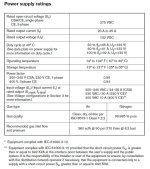